You’ve invested time into researching many aspects of PLC (programmable logic controller) automation and are now ready for your first project. Here are a few pointers to help you proceed.
The good news is that there are many great products and resources available to help when you are ready to embark on your first automation project. The challenge is that automating equipment, machinery and systems with PLCs and other devices is a multi-faceted endeavor.
To successfully execute an automation project, end users must be ready to take on the following duties:
- Understanding the equipment or process functions
- Accounting for mechanical real-world behaviors and interfaces
- Ensuring the equipment is properly instrumented
- Designing control panels
- Designing electrical power and I/O wiring
- Developing drawings and documentation
- Planning for installation and constructability issues
- Communication interfaces
- Creating and testing PLC programming
- Configuring HMI displays useful for operators
- Testing the system to ensure it runs for the long haul
Very few people can do all these tasks well, so most likely you will delegate at least some of the tasks, with the team coordinating as required. Of course, sticking to a materials and labor budget to execute the project is important, so usually there is a project manager keeping an eye on those items.
Following are a few tips for your first PLC project.
Plan the Work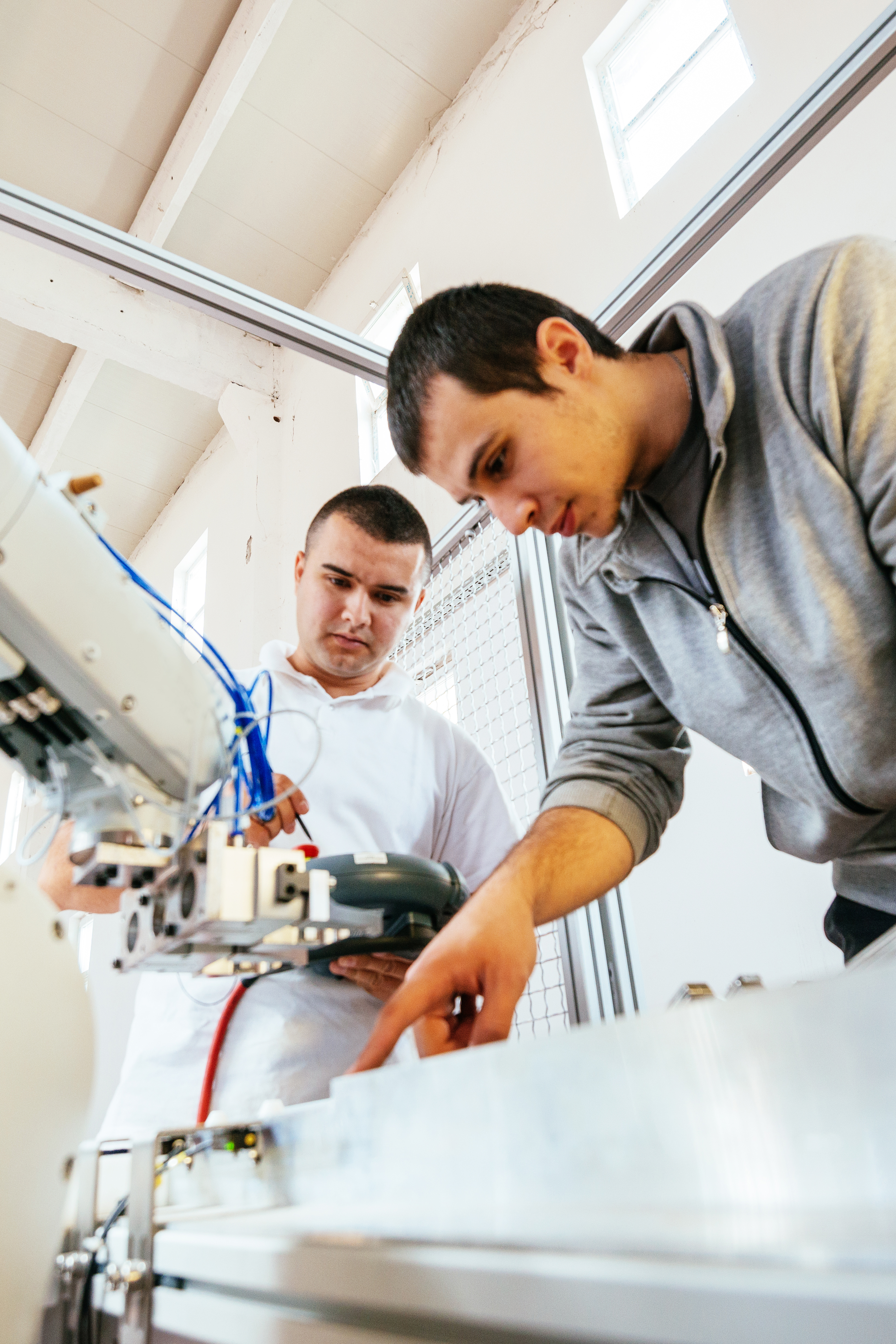
Whoever understands the functionality must document it in a way others can understand. This might be a written sequence of operation, a functional description, a flow chart, a list of steps, or any other useful method. This documentation provides the basic requirements that the team will follow for design and testing.
Expect the Unexpected
Design for real-world situations, not perfect scenarios. Normal operation is relatively simple for many applications, but developing a system that is resilient when problems happen is much harder. Think about how the equipment can fail, get jammed, operate too slowly or be subjected to operator errors, and build in provisions or even manual features to handle those situations.
All About the I/O
A control system is only effective when it can monitor the right conditions and command the right actions. Early on, create a complete I/O list to indicate how every point of control operates (normally open, normally closed, energize to open, etc.) so the team is working with a common understanding. Add more sensors and I/O when you start out than may be needed because it is always easier to delete than add down the road.
Keep the Crew in Mind
Designing control panels and electrical schematics is detailed technical work subject to UL and NEC requirements, and will require qualified design and engineering support. However, a good common-sense practice is remembering those who will work on these systems in the future. Make the documents and drawings good enough so future personnel can figure out how the system is put together. Provide enough working space, good tagging and troubleshooting aids to help installers, operators and maintenance personnel do their jobs.
Spares, Spares, Spares!
For new designs, always build in spares and future space to the greatest extent practical — most people target about 25% installed spares as a good rule of thumb to address possible changes. If you will be producing a typical system over and over, you can shave down these spares when you go into production. Order extra consumables like fuses, and consider stocking some additional devices like circuit breakers and terminal blocks so changes or fixes can be made quickly.
Pre-Check the Tech
Classic hardwiring and I/O are relatively straightforward. However, more complicated connections using industrial communications may take some extra effort to ensure everything is compatible. Most products play well together, but it’s always a good idea to pre-check these links early on the test bench to make sure all drivers, tag names and addressing are working as expected.
PLC and HMI Programming is Crucial
Programming PLCs and HMIs can be the most intensive part of the automation effort and is the most unlike the rest of the tasks. It is very hard for most people to determine the status of software as it progresses from 0 to 100 percent complete. Hold progress meetings often. Document the code exhaustively, especially making sure that every I/O point and variable has a human-friendly description. In fact, consider cutting-and-pasting the requirements into the program comments, and adding more comments to explain what is going on.
Test Early and Often
Test your software work on the desktop piece-by-piece as you develop it, and section-by-section as you combine routines. Create a detailed test plan based on the requirements documents and execute that plan in shop conditions before you go into production. Dream up crazy conditions to “stress test” the code. Then test everything again the same way when the system is installed in the field.
Pulling it All Together
The preceding tips should help as you work through the details of your application. Fortunately, industrial automation is a mature field and there are many great commercially-available hardware and software products to make your work easier. With due diligence, you will soon stand back and admire your automated system in action!