Having an edge-connected factory allows you to access your data at anytime, on or off the factory floor. No more manual reports, no more wondering what’s happening on the factory floor while you’re away. You can track efficiencies and identify weak points in your factory as well as bring together data from multiple sites to manage resource distribution and maintenance and compare performance across facilities. Sounds great, right?
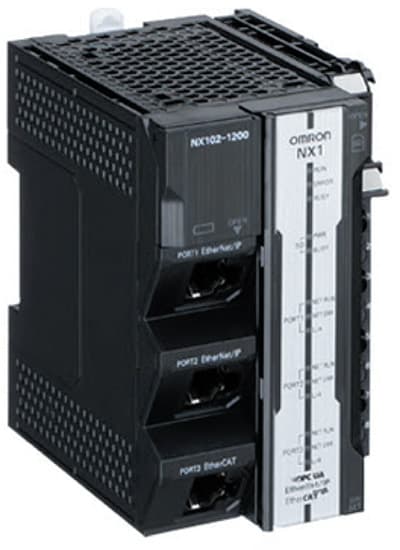
Even better, you don’t have to start from scratch. Building an edge-connected factory does not require replacing all your legacy equipment—whether you have a system based on PLC-5, S3 or a cutting-edge ET 200SP or NX102. You can still use your existing field devices, network connections and controllers to build an edge-connected system and create custom dashboards from multiple data streams for every level of user at every level of the business. Capture low-level data for maintenance and continuous improvement. Create a high-level dashboard for operation managers to monitor facility output and keep processes moving smoothly. To keep all stakeholders informed and up to date, you can create a feature-rich visualization system users can access from anywhere with an internet connection.
Because a cloud system is based on data, not hardware, the system is brand agnostic. Your factory equipment does not need to be on one type of fieldbus and you can add pieces quickly and cost-effectively, with data behind your decisions.
Download our Engineering.com whitepaper, “Bringing Your Factory to the Edge in 2021,” to learn the details involved in converting your legacy equipment into an edge-connected system—the layers of components and connectivity involved as well as edge architecture choices—plus the advantages that come with this digital transition. You will understand how an edge-connected factory can enable you to view and harness your production data and make it work for you, and you’ll see how this digital transition is within reach.