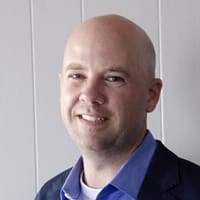
Brendan Cavanagh
Vice President of Sales, NYCO
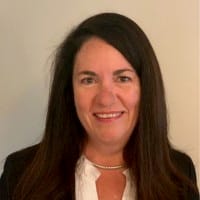
Julie Samsel
Channel Marketing Manager with ITW Pro Brands
RS’s “Ask The Expert” series taps into the experience and expertise of key thought leaders and subject matter experts from the more than 500 global suppliers we work closely with to bring customers solutions for their most challenging problems (and the daily ones, too).
In this edition, we talk with RS suppliers in the facilities maintenance space including Brendan Cavanagh, Vice President of Sales from NYCO and Julie Samsel, Channel Marketing Manager with ITW Pro Brands (SCRUBS, DYMON, Spray Nine) to understand the latest in facilities maintenance products and technology, particularly as businesses address a post-pandemic return to work.
What’s new in cleaning and sanitation tech?
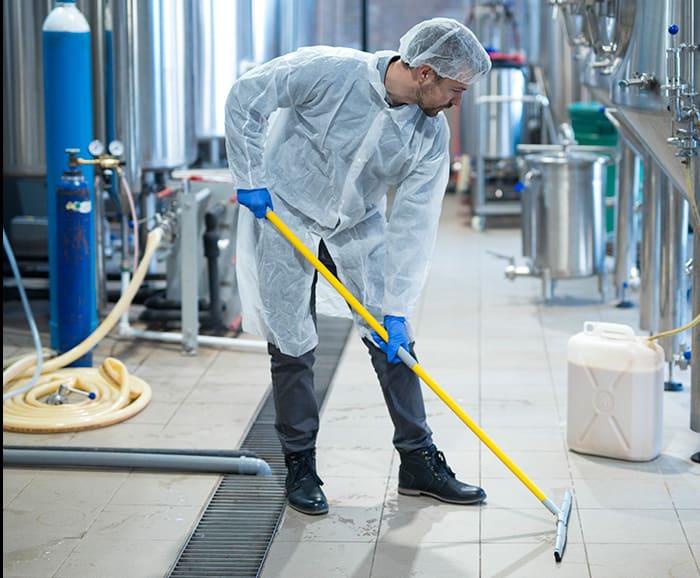
Brendan: Over the last year plus, there is a lot of new technology with electrostatic sprayers and disinfecting. Many users now understand that they should look at disinfectant labels for dwell times and make sure the product kills the appropriate viruses and bacteria. This has led to increased overall awareness in the cleaning segment of choosing the right cleaning and disinfecting products and equipment for a particular area or situation. With cleaning for health and safety now at the forefront, the technology of disinfectants and how to apply them is really in focus. NYCO’s new Hydrogen Peroxide Disinfectant (HPX) disinfectant is an example of a relatively new technology – hydrogen peroxide disinfecting – which is safer for the user and more environmentally friendly than many other methods. As a timely bonus, HPX happens to kill the COVID-19 virus with a very short dwell time of just 1 minute.
Julie: We are also seeing demand for disinfectants with quick kill COVID-19 capability. It makes sense that businesses care about how effective a disinfectant is in today’s post-pandemic world, and these quick-kill claims have the added benefit of reduced time to clean and disinfect. Another trend that we are seeing in cleaning and sanitation technology is a move towards environmentally friendly and more sustainable options. Customers are looking for refillable containers and moving towards large area disinfection equipment.
What’s the toughest customer challenge you’ve seen and how was it solved?
Julie: With the pandemic, many of our customers had to quickly pivot to new cleaning protocols. Several of our customers need to disinfect large areas under severe time constraints. A great example of this problem is the interior of a commercial aircraft. We were able to help our customers by providing Celeste Sani-Cide EX3 Disinfectant and Multi-Purpose Cleaner applied through an electrostatic sprayer. It’s the perfect solution for a quick disinfection of a large area in a short amount of time. We’re very customer-focused and result-driven here at ITW, and we are pleased to be able to offer these solutions through our partners like RS.
Brendan: The toughest challenge for end-users now, whether they are industrial facilities, schools, nursing homes or offices, is how to provide a safe environment for employees and building occupants. We have helped customers overcome this by working with our distributor partners like RS on training for health and safety protocols for cleaning and disinfecting. You see this concept incorporated into advertising by professional sports teams, hotel chains, and airlines — who showcase how they are cleaning for the health and safety of their customers and employees.
Businesses can solve this challenge by having a written plan and protocol in place, not only for the return of employees and occupants, but also for how they will handle any potential outbreak situation from a future virus. Organizations need to always be aware of current federal, local, and state guidelines. We can help educate and train customers to properly implement recommended cleaning and disinfecting procedures, as well as on which products work best for which applications.
How should facilities managers think about balancing value, cost and performance when buying cleaning products and equipment?
Brendan: I think the balance of performance versus cost, first and foremost, needs to prioritize employee safety. The cleaning industry is at the forefront of safety, comfort, and confidence in how an employee feels at work, especially when returning for the first time post-pandemic. Facility managers need to take a strong look at the cleanliness of their environments and the awareness and information they are providing to occupants. At NYCO, we disinfect all high-touch and high-contact surfaces routinely throughout the day, as well as ensuring hand sanitizer is readily available. Every employee is provided disinfectant solution to use at their workstations. These are the things we would also recommend for facility managers whenever possible.
When facilities are clean and healthy, it makes employees feel more valued by their company, and helps people stay healthier overall. I think the time has come, and it’s a good thing, that cleanliness and sanitation are at the forefront of the value discussion. Cleanliness brings great value to organizations and is no longer viewed as an expense that can be cut.
Julie: Price should not be the only deciding factor in cleaning and sanitizing. There are many factors to consider, including product safety, environmental concerns, packaging options, product longevity, performance, and process improvements. It is important that facilities managers are open to new technologies in equipment. Often customers will see greater benefit if they look less at the cost to buy and more at the cost to use.
How important are environmental and sustainability concerns for facilities managers when selecting cleaning products and equipment, and what are suppliers doing to help address those concerns for customers?
Julie: Environmental, safety, and sustainability concerns are growing within many markets and expanding year-over-year. One of the greatest challenges for suppliers is providing high-performing, affordable products that meet customers’ expectations. Formulation development requires balancing the raw materials currently available to craft sustainable and EHS-focused goods, with our high standards for providing quality products and equipment—all while keeping prices reasonable.
Brendan: Environmental and sustainability concerns are very important today. Many facilities like schools, day care centers, and LEED-certified buildings put a high priority on sustainability. Cleaning product manufacturers and distributors need to be able to train and help customers choose cleaning products that meet both sustainability and efficacy requirements.
There are several aspects of sustainability that users should consider. Dilution control systems – like the NYCO ez2mix dispensing system– give users the ability to use precise dosing of chemicals, which eliminates waste. These types of systems with concentrated chemicals reduce packaging and save on transportation costs which decrease carbon footprints and help the environment. Dilution control systems are also safer for users, since people have less contact with the actual chemicals.
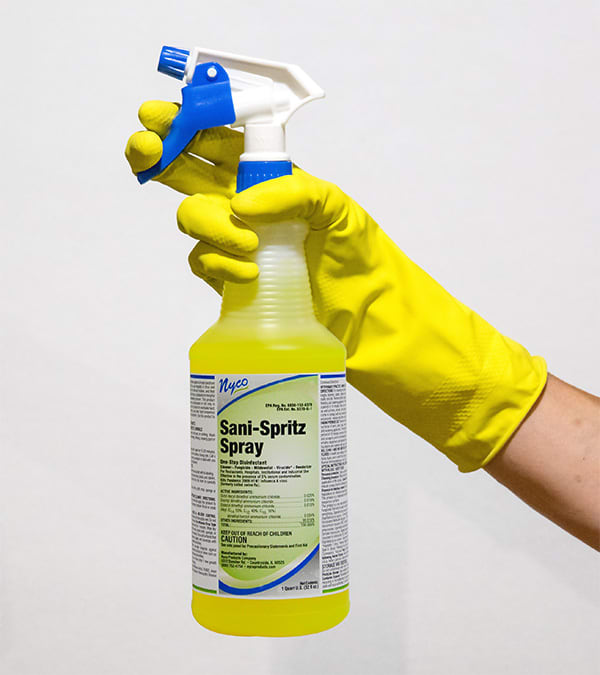
One very safe and sustainable RTU disinfectant is our new HPX Cleaner. The sustainability aspect comes from the hydrogen peroxide chemical formulation H2O2, which breaks down into water and oxygen once sprayed, so there’s no residual chemical left on the surface. It is entirely safe for surfaces and people. In fact, you don’t even need to wear PPE when using it.
How should facilities managers think about cleaning/sanitation differently in a post-COVID environment? What new/different products and equipment will facilities managers want to have on hand as more employees return to workplaces in the coming months?
Brendan: As employees, customers and students start to re-enter buildings, facilities managers should take into consideration many factors to establish and maintain a high standard of health and safety for employees and occupants including, “touch-free” facilities; daily disinfecting and cleaning procedures, especially for high-touch surfaces like doorknobs; easily accessible hand sanitizer stations for all occupants; and protocols to handle outbreak situations.
All the above considerations should be detailed in written standards and procedures with everyone on the same page, and then contractors and other visitors can follow them too. Once standards are written, facilities should monitor, measure, and validate. ATP testing is one option for that.
For certain, facilities should make sure they have an increased supply of disinfectants that are not only approved for use on the COVID-19 virus, but also kill a broad spectrum of viruses and bacteria. I think occupants of buildings are looking for no-contact, hands-free solutions, particularly when it comes to hand sanitizer dispensers and hand soap and hand towel dispensers.
Julie: Facility managers should have employee health and safety as a high priority. That’s not limited to physical safety and injury prevention, but also focusing on protecting their employees against infectious diseases. It is not just the common cold and the flu anymore, but more severe diseases, like COVID-19, that are easily transmitted throughout a facility can bring production to a halt. Disinfection products and programs are the new standard and should not be neglected as this pandemic wanes. Besides hand cleaning and surface sanitization programs and associated products, facilities management should be looking into mass disinfection equipment, products, and facilities construction to support the health and well-being of their employees.