RS expert Jeff Clonts addresses electrical connectivity trends, components and fundamentals and shares key design considerations for engineers, machine builders and panel builders.
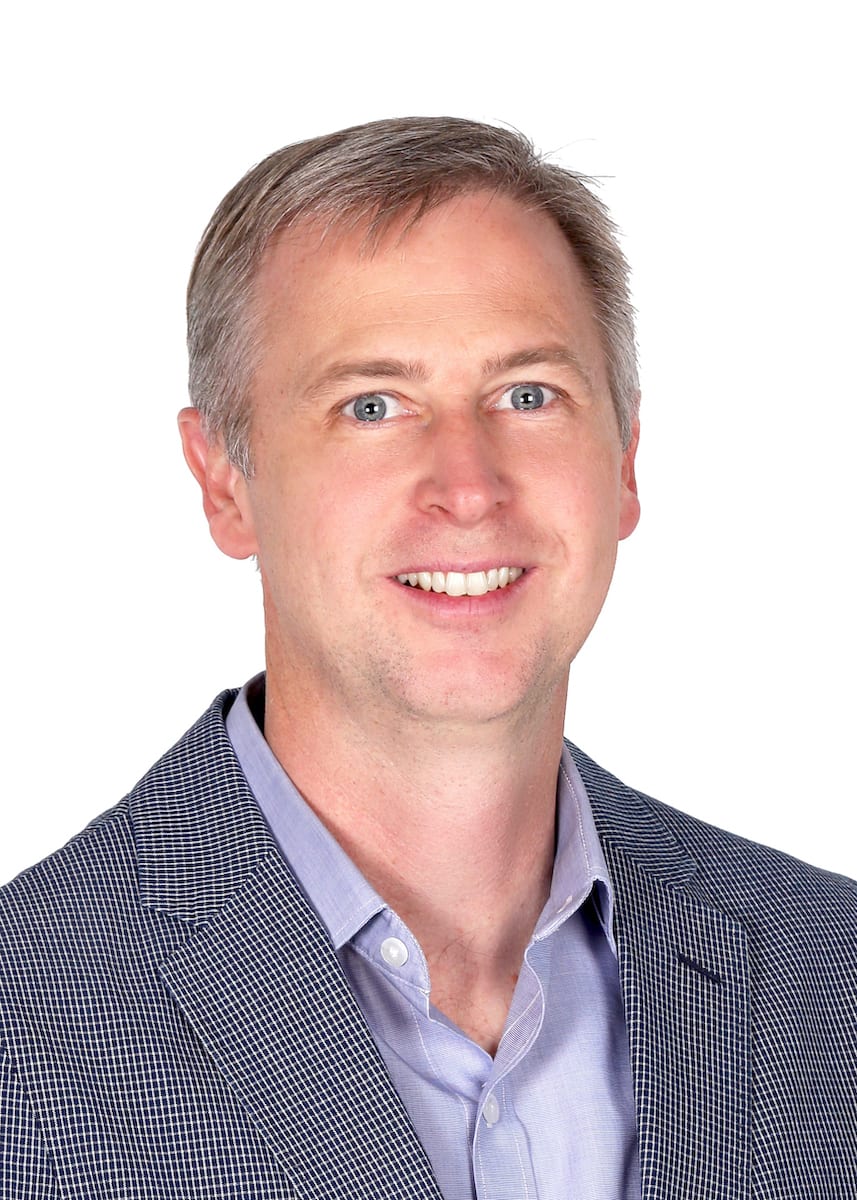
In this latest installment of RS’s Ask the Expert Series, Technical Support Manager Jeff Clonts talks about electrical connectivity trends, components, fundamentals and standards and shares key considerations for designing machines, building control panels and replacing parts.
Hi Jeff. How did you come to work in the electronics industry and what current connectivity trends are you most excited about?
My background in this industry started in maintenance and repair and panel building and installation for various integrators and manufacturing facilities. About six years ago, I moved into the distribution side of the business. One of the connectivity trends I’m currently excited about is the increased availability of push-in connectors. Push-in connection technology provides quick, easy and reliable connections for controllers, I/O modules, terminal blocks and more without any tools. The industry is trending toward this design due to the speed of installation as well as the high-performance, vibration-resistant electrical connections these push-in connectors provide.
We hear the terms electrical connectivity, electronic connectivity and industrial connectivity used frequently. Can you explain the differences?
Sure. Electrical connectivity is all about power — sending electrical current from an energy source like a wall outlet to the components in a device or machine that use this electrical energy to perform a task. “Electrical” and “electronic” are words that are easy to mix up. Electronic connectivity refers to using or directing that electrical current in a way that sends information back to the user, often through an electronic display panel. A simple example would be a digital home thermostat that’s powered by electrical current but then uses that current, along with other components, to show you the temperature of your home, allow you to adjust the settings and convey alerts.
Industrial connectivity involves all of the components used to deliver power, control signals and data in industrial applications like manufacturing facilities. And then network connectivity transmits that data to an endpoint where an operator, manager or technician can read it and take the appropriate action.
There’s definitely overlap, though, and I think that’s where the confusion sometimes happens.
Every machine that runs on electric power requires electrical connectivity solutions including connectors, wires and cables. What are some of the connectivity components that designers, machine builders and maintenance technicians rely on most?
Machine builders rely on various industrial connectors and cable assemblies to build their equipment or automated systems — most notably, machine tool wire (MTW), equipment wire for power and control circuits inside the control panel. MTW is available in various sizes and color options, but panel builders should stick to the appropriate NFPA 79 wire color codes when selecting wire colors for control panel circuits. Panel builders must also comply with all NEMA requirements for selecting the correct conductor size for each electrical circuit.

The NFPA 79 Electrical Standard for Industrial Machinery is one of the most important industrial equipment standards in North America because it provides safeguards that protect operators, equipment, facilities and products from fire and electrical hazards. This standard applies to all of the electrical and electronic elements in industrial machinery, including injection molding machines, assembly, material handling, inspection and testing equipment and machine tools that operate at 1,000 V or less. NFPA 79 also sets the standard for how to properly wire and ground industrial machines and equipment including control panels.
RS has a great selection of MTW equipment wire and other NFPA 79 wire and cable from leading connectivity manufacturers.
Speaking of NFPA 79 compliant wire, hook-up wire is prevalent in low-current, low-voltage electronic applications. What are some important considerations when specifying hook-up wire?
Anyone wiring an enclosed piece of electronic equipment — such as control panels, meters, appliances and automobiles — will need hook-up wire. This insulated, single-conductor wire can also be used in marine applications, building construction, electrical circuits, motors, transformers, switchboards and rectifiers.
Hook-up wire comes in many different gauge sizes and voltages and is available with a variety of different insulation materials and with solid (single-wire strand) or stranded (thin, bundled strand) conductors made of bare or tinned copper, the latter of which exhibits robust resistance to corrosion in high-temperature, humid and/or wet environments. Many types of hook-up wire also meet UL and MIL-spec standards in addition to NFPA 79 requirements and, in most cases, hook-up wire is classified according to its insulation material.
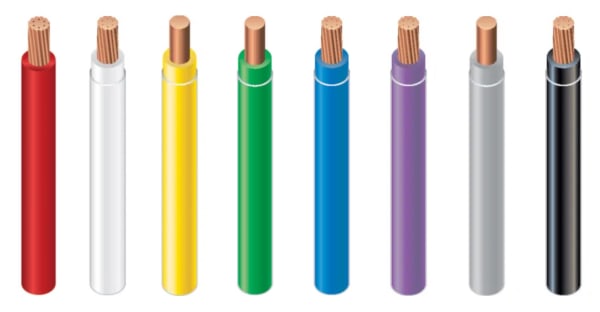
Insulation, or wire jacket, choices typically include PVC, PTFE/Teflon, neoprene and silicon rubber, but PVC jackets are the most common because of their low cost, durability, wide range of uses and rugged resistance to moisture, chemicals, abrasion and impact.
As far as sizing goes, the most common hook-up wires are 22 AWG and 28 AWG. And most hook-up wire is rated at 600 V or less or 1 kV or less.
Electrical connectors are crucial for ensuring that power supplies are steady and reliable. How do design considerations around connectors vary across applications?
Many industrial applications, including factory automation, food and beverage processing and automotive manufacturing, will use similar connectivity components inside the control panels but have different requirements for the cables and connectors outside of the enclosures. Equipment installed in harsh environments will require different levels of protection against hazards including water, dust, dirt, corrosion, oils, chemicals and flammable gasses, so it’s important to select the correct IP and/or NEMA rating for the conditions at hand.
For example, automation connectors intended for use in industrial applications are designed to withstand a wide variety of harsh environment conditions. This makes them ideal for use in applications including food and beverage processing, automotive production, manufacturing, robotics, commercial vehicles, military and agricultural equipment and even valves and pressure switches.
RS supplies two main types of automation connectors: M series circular connectors, like M8 and M12 connectors, and DIN valve connectors. M series connectors are multi-pin connectors optimized for sensor and automation applications. They form extremely resilient, reliable seals when mated and are often equipped with IP65, IP67, IP68 or IP69k sealing. DIN valve connectors also enable easy installation and are widely available with IP65, IP67 or IP68 sealing.
In general, most connectors come in a variety of shapes, sizes, materials, pin counts, IP ratings and electrical specifications. So, it’s important to consider application requirements including the application environment, reliability, durability and ease of installation when specifying connectors.
Do variable frequency drives require a VFD cable, or would a standard cable suffice?
Variable frequency drives (VFDs) are comprised of three main subsystems — an AC motor, main drive controller assembly and drive/operator interface — and are used in motor control applications including conveyor systems, complex industrial machines and robotics. VFDs control motor speed and enable smoother starts and stops, which is key for precise industrial applications, but they can also cause electrical noise and voltage spikes. Using a VFD cable instead of a standard cable ensures better performance and reliably protects sensitive electronic components from potential damage.
VFD cables are shielded to prevent the electrical noise and voltage spikes caused by VFDs from damaging motors. Standard cables subjected to stray voltages could break down and fail. VFD cables are typically equipped with copper or aluminum shielding material that wraps around the conductor in a foil or woven braid design that helps optimize the performance of both the drive and motor. These cables are commonly rated for 600 V, 1 kV or 2 kV, and the higher the voltage rating, the more insulation they have.
Cables in control panels and industrial equipment can be subjected to quite a bit of stress, especially around the connections. What tips do you have to help customers find the appropriate strain relief or cable gland?
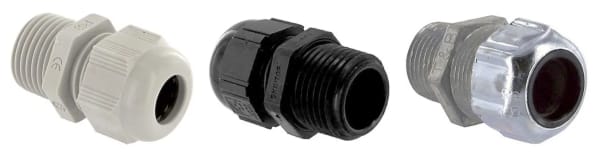
Thinking about how electrical cables are going to be protected is an important part of the design process for control panels and other industrial equipment. Strain relief components, as they’re called in the U.S., or cable glands, as they’re called in Europe and other parts of the world, are key to protecting cable connections from stress. These products secure cables to panels and connectors and prevent mechanical forces from breaking the conductor inside of the cable or disconnecting the cable from the connector.
With pre-manufactured strain reliefs, you simply slip the strain relief over the cable before the connector is terminated. These economical strain reliefs are then attached to the connector assembly with a screw or glue. Custom-designed strain reliefs provide better moisture protection, tensile strength and flex life and can be overmolded onto the cable for peak protection or slipped onto the cable like pre-manufactured versions.
Dome-style strain reliefs protect cables entering the equipment and flex-style strain reliefs have a spiral shaped spring wrapped around the cord that adds strength to the cable at the connection point, where it is most vulnerable to damage, and prevents it from kinking.
Which applications are terminal block connectors best suited for?
Terminal block connectors are typically modular and designed to be mounted on DIN rails to enable high-density connectivity. They are widely used in motion and automation control systems to provide safe, reliable connections between multiple electrical wires and circuits. Terminal blocks keep these connections secure and control panel wires well organized, which achieves a clean, professional look and makes maintenance much easier and more efficient.
Since electrical connectivity is all about power, are there any closely related power topics you’d like to touch on?
Power supplies are a critical part of electrical connectivity systems. Panel builders working in control panels that use DIN rails to mount circuit breakers, terminal strips, sensors and other electronic components will need a DIN-rail power supply. DIN-rail power supplies are typically switch-mode power supplies that convert incoming, unregulated line power into regulated DC voltage that can be used by industrial automation equipment and are often chosen for their compact design, light weight and high efficiency. However, heat dissipation can be an issue since they’re enclosed, so panel ventilation is critical for peak performance.
Machine builders, on the other hand, often prefer open frame power supplies. Open frame power supplies are not enclosed, which means that they’re easier to keep cool, subject to fewer configuration constraints and typically more compact than enclosed power supplies, but they don’t offer protection against environmental hazards. So, they aren’t a good choice for applications exposed to dust or moisture unless they’re sufficiently protected by other equipment.
When choosing a power supply, you’ll want to factor in all of the elements that affect heat dissipation, including the space surrounding the power supply, mounting position, heat generated by nearby electronic components, the applied load, ventilation and cooling.
Another important power topic closely related to electrical connectivity is protecting machines, equipment and products from power surges and dirty power.
Voltage transients, sags, surges, electrical noise, harmonic distortion. grid and facility power interruptions and brownouts can damage electronic components and lead to system failures.
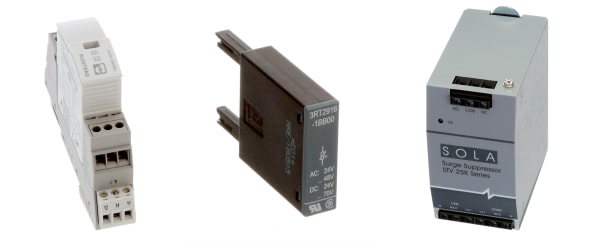
So, power protection is crucial. Solutions include surge protection devices designed to protect connected equipment from sudden power surges. uninterruptible power supplies designed to provide second-level protection against power surges and a battery backup so connected systems can be shut down safely and power conditioners designed to “clean” power by reducing the amount of electromagnetic interference in the power line.
Surge protection is another requirement of the NFPA 79 Electrical Standard for Industrial Machinery. In addition, surge protection devices must be UL listed and their short-circuit rating must match the short-circuit current at the point of installation.
Why should customers come to RS for electrical connectivity solutions?
RS offers more than 3,000 electrical connectivity products — including more than 1,500 ready-to-ship electrical connectivity solutions — from industry-leading suppliers including Hubbell Wiring Device – Kellems, Pass & Seymour, Leviton, SCHURTER and Superior Electric, and you can filter our vast collection by manufacturer or connector type.
Another benefit of sourcing electrical connectivity solutions from RS is our RS Pro by RS line of private label products, which offers a variety of electrical and electronic connectors. This vast selection of quality products is designed for use in various electronic and automation applications and is rigorously tested, attractively priced, compliant with all relevant international standards and well stocked at our Fort Worth distribution facility. In addition, all our RS Pro products are backed by the RS Pro Seal of Approval, which is only awarded after a meticulous quality control process based on stringent international standards.
RS also prides itself on providing comprehensive, end-to-end electronic, industrial and automation solutions and offers more than 3.5 million products from over 650 trusted suppliers, as well as a comprehensive suite of services and tools including a highly experienced technical support team, kitting, bagging and labeling services, a BOM tool and an online registration page featuring helpful information and how-to guides including a Quick Start Guide, a guide to Advanced Features and an FAQ.
For more information about RS’s extensive portfolio of electrical connectivity solutions, please visit the links embedded throughout this article. For assistance identifying and deploying electrical connectivity solutions optimized for your unique application, please contact your local RS representative at 1.866.433.5722 or reach out to technical support team.