Facility managers and intralogistics professionals face common challenges, including unplugged frontline workers and investment and security hurdles. Mark Russell, Technical Application Support Manager at RS, explains how Industry 4.0 solutions can help, shares tips for getting started, and introduces a few solutions to consider.
Mark Russell, Technical Application Support Manager, RS
For those who manage facilities and intralogistics, their decisions are only as good as the information they have to work with. If data is inaccurate, inaccessible, outdated, or delayed, processes within an operation can’t operate at their best.
Facility management and intralogistics span a broad range of realms — everything from information flow and risk management to supply chain monitoring, inventory control, and distribution workflow. It also encompasses many industries, including transportation, warehousing, retail, and entertainment.
More and more, these intricate, dynamic systems are relying heavily on digital tools to deliver data and information, which can impact manufacturing considerations like order fulfillment, customer satisfaction, and staffing allocations.
Many companies are evolving by undergoing digital transformations to better take advantage of what’s to come. The global logistics automation market is projected to grow from $78.20 billion in 2024 to $212.81 billion by 2032.
With so many moving parts related to facility management and intralogistics, staying relevant with the latest technology can be challenging, but it doesn’t have to be when using the right partners and resources.
How Industry 4.0 & IIoT Fit Into Facilities and Intralogistics
Industry 4.0 advancements include electrification, digitalization, automation, remote condition monitoring, predictive maintenance, and advanced data analytics. Ultimately, it’s about helping businesses run more efficiently. Data and information drive these advancements. “Investments in emerging technologies, such as artificial intelligence, end-to-end visibility and advanced automation are expected to drive competitive advantage and greater resilience to future disruption in the logistics sector,” according to the 2024 State of Logistics Report.
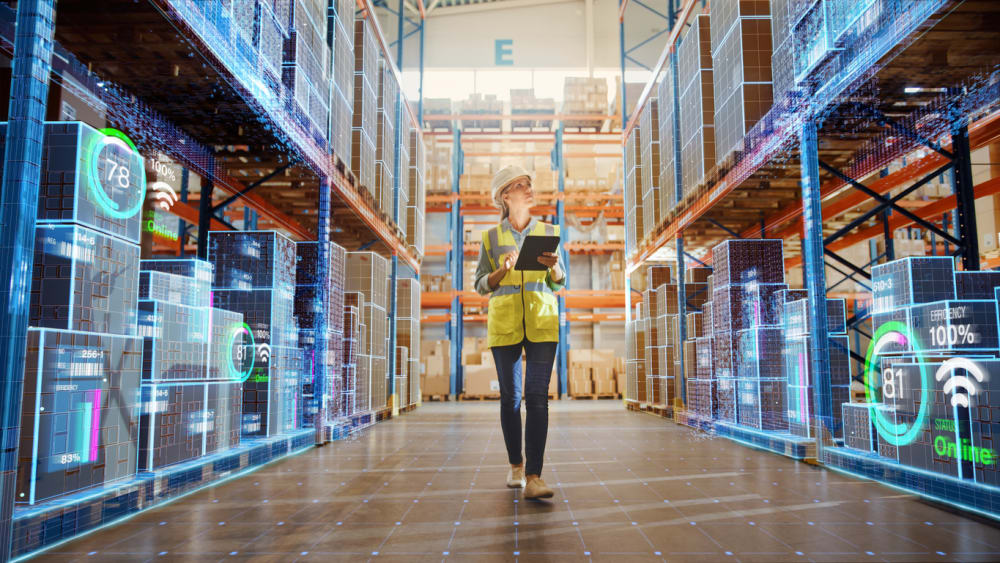
These transformations go hand in hand with connectivity, and that’s where Industrial Internet of Things (IIoT) devices can play a vital role. IIoT devices collect data, which can then be transmitted or shared with other systems and devices like process controls and monitoring systems for further usage.
According to Inbound Logistics, some of the ways that digital tools can improve facilities and intralogistics in a variety of industries, including retail and entertainment, warehousing and distribution, and transportation infrastructure, like ports:
- Real-time shipment tracking, which can help with location monitoring and route management
- Inventory management to monitor and evaluate stock levels and supplies
- Vehicle tracking to help manage fleets and routes
- Predictive maintenance to better plan downtime
Once a business decides to take part in the digital evolution, the opportunities are endless. Some technologies revolutionizing logistics include goods-to-person (GTP) robots, automated storage and retrieval systems (AS/RS), automated case erectors, automated packaging systems, and augmented reality (AR).
Unplugged Frontline Workers and Remote Locations
Many facilities rely on frontline workers — those working in operational functions, such as interacting with heavy machinery, packaging lines, or ride controls. They often aren’t at a desk consistently while on the job, and they may not routinely interact with a computer or device while performing their job.
While many intralogistics solutions rely on digital processes, this leaves a gap between those who are online throughout the day and those who aren’t. The facility, as a whole, is impacted by reduced engagement and job satisfaction from frontline workers, along with a disparity in awareness and knowledge of the system.
Solutions designed with the frontline worker in mind can help combat this issue. This can include creating a digital home base where employees can access important information and utilizing mobile-friendly applications or remote monitoring, so frontline workers can more easily observe machinery.
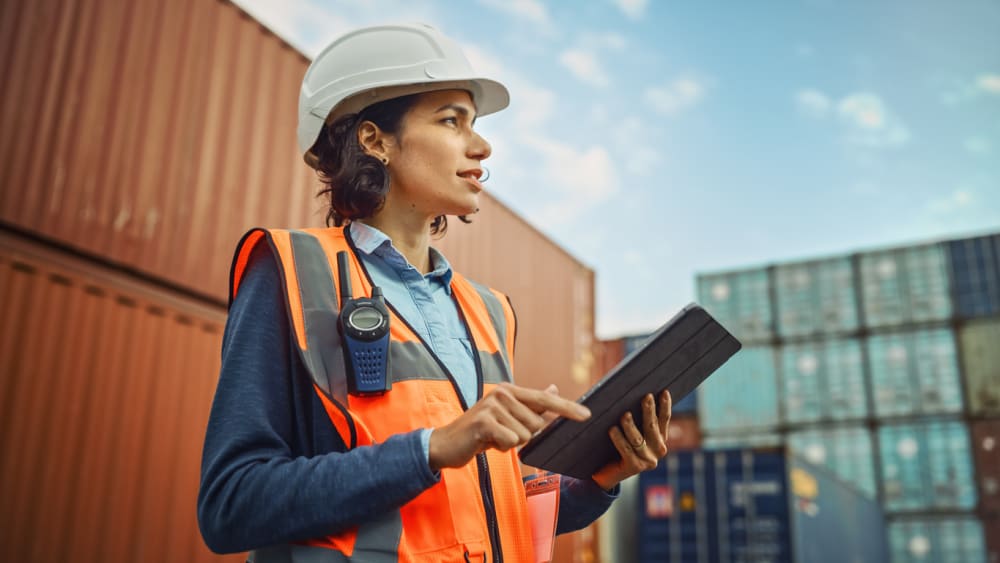
Another growing trend is the number of remote workers who are involved in analyzing data but may not be in the same location as the facility itself. Smart systems have the ability to share data in a way that’s easy to review, analyze, and communicate with features like cloud-enabled data sharing. Improved condition monitoring also means better predictive maintenance, resulting in a safer environment for all equipment and employees.
Yet, while the benefits of digitalization range from reducing downtime to optimizing personnel staffing and workload, many businesses face challenges regarding selection and implementation.
Knowing Where to Start
For those just stepping into the world of IIoT, the learning curve can feel intimidating. Knowing where to start can be tricky, and many companies rely on legacy or outdated systems that aren’t compatible with the latest digital tools. Fortunately, many solutions can seamlessly fit into existing systems without having to overhaul everything.
According to Inbound Logistics, facility managers and intralogistics professionals looking to adopt Industry 4.0 digitalization technologies like IIoT devices should:
- Identify key areas: Find the places in your business that will benefit the most from added capabilities, like inventory or fleet management.
- Start pilot projects: Test IoT systems on key areas at a smaller scale before implementing them across your business.
- Utilize modular systems: Develop a scalable IIoT infrastructure with the ability to grow and change as needed, selecting solutions that meet interoperability and cybersecurity requirements.
- Identify security risks and put a plan in place: Anytime a device is connected to the internet, the risk of security breaches comes into play. A robust cybersecurity plan utilizing up-to-date tools — such as encryption, firewalls, virtual private networks (VPNs), and secure storage — can help ensure the safekeeping of sensitive information.
Many reputable companies provide hardware and software solutions specially designed to be easy to install and commission. Other resources make developing project ideas into real innovations utilizing the latest technology easier, like OKdo, a curated product line featuring top brands with cutting-edge embedded technology. Through partnerships with companies like NVIDIA, Intel, Arm, Arduino, and Coral by Google, this range offers the latest in emerging technologies, spanning artificial intelligence (AI) that enables machines to perform advanced tasks to IIoT and edge computing.
Investment Hurdles
Upgrading a system, of course, takes time and capital — from the price of new solutions to training and deploying the changes. According to the 35th Annual State of Logistics (SoL) Report, “total U.S. business logistics costs for 2023 were $2.374 trillion. While that number seems high, it actually represents an 11.2% drop in total logistics costs from 2022.”
Inbound Logistics suggests developing a strategy from the beginning that focuses on business goals, objectives, expected outcomes, and metrics to help dictate when and where certain solutions should be implemented.
By choosing products that are easy to integrate, you can better utilize new technologies while still working within your existing systems and infrastructure. By avoiding data silos, you can ensure that the information digital tools like IIoT devices glean from your system is readily available, shareable, and actionable.
Edge computing solutions, for example, not only bridge the gap between information technology (IT) and operational technology (OT); they can also take readings from both older and newer devices and send that data to the cloud or local control systems for further analysis, allowing businesses to track data and trends like never before.
“With the right edge computing devices, disparate devices and protocols that previously could not communicate with each other now have a translator,” said Joe Wagner, Field Application Engineer at Red Lion.
Other emerging areas in facilities and intralogistics include Open Platform Communications United Architecture (OPC UA), a machine-to-machine communication protocol designed for secure and interoperable data exchange with enterprise-level and cloud-based systems, and time-sensitive networking (TSN), a standardized framework for data transmission and network traffic management that improves Quality of Service (QoS), meets increased Ethernet demands, and propels IT-OT integration in industrial automation environments. Simultaneously running Ethernet-based protocols like OPC UA and PROFINET over TSN technology helps create convergent networks that are reliable, scalable, and flexible.
Industry 4.0 Solutions for Smarter Facilities and Intralogistics
There are tons of readily available, user-friendly, and field-proven Industry 4.0 solutions for facility managers and intralogistics professionals looking to embrace digitalization and enjoy the many advantages it offers, and they all have one thing in common: data. Facility managers and intralogistics professionals in every industry — spanning warehousing and transportation to retail and entertainment — all rely on accurate, real-time data to make the best decisions about things like risk management, inventory control, and distribution.
Industry 4.0 has evolved to a point where most systems, machines, devices, and components can be interconnected. Reviewing current infrastructure will allow you to identify areas where updated technology can help optimize output and better achieve goals, such as improving modularity, scalability, or interoperability or adding remote monitoring. We recommend considering smart PLCs, industrial PCs, sensors, and motor drives to support facility and intralogistics advancements.
PLCs are small industrial computers that receive data from properly interconnected IIoT devices, like sensors, and use that data and internal logic programming to control and automate system processes. These small industrial computers are typically installed directly on machinery and, as such, must be ruggedized. Other optimal characteristics include high reliability, ease of programming, and fault analysis diagnostics. I/O solutions, like connectivity solutions, help link IIoT sensors to PLCs and other controllers.

Phoenix Contact PLCnext Controllers are the hardware component of the company’s PLCnext Technology ecosystem for industrial automation. Engineered to help users contend with the challenges of digitalization and globalization, this open automation ecosystem supports flexible, modular expansion for future-proof utility in a variety of markets and enables implementation without the limitations of proprietary systems. PLCnext controllers are based on a Linux kernel and characterized by their real-time capabilities for both standard IEC 61131-3 programming and higher-level programming languages — such as C/C++, C#, and Matlab Simulink — as well as their patented task handling capabilities, which enable the parallel combination of IEC 61131-3 code, high-level languages, and model-based tools in a single task.
These smart controllers also support cloud connectivity, making it easy for onsite and remote workers to access system data critical to optimizing processes and — in turn — improving quality and reducing costs. And since they handle sensitive data and are often employed in harsh environments, they offer both digital and physical protection, including TÜV certifications (in accordance with IEC 62443-4-1 ML 3 Full Process Profile and IEC 62443-4-2) and IP20 form factors. Users can choose from a wide range of I/Os or extend the PLCnext Control interfaces and functionality with left-aligned modules, including options capable of implementing AI or edge applications. Their open Linux core also allows users integrate new technologies, such as OPC UA, TSN, and Industrial 5G.
Industrial PCs are another solution ideal for implementing and improving data-informed decision-making in facility and logistics operations. These tangible counterparts to cloud computing platforms are available with a variety of interfaces and add-on modules that allow users in various industries to collect, visualize, process, and act upon real-time device, equipment, and facility data, which is vital to improving organizational responsiveness and efficiency and reducing operating costs.
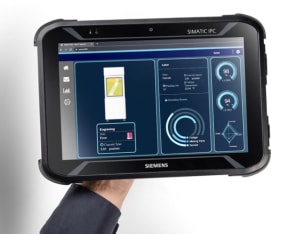
Siemens SIMATIC IPC MD-34A industrial tablets put all those capabilities in the palm of your hand to optimize mobile productivity. These next-gen. industrial PCs have a ruggedized, lightweight, and modular form factor equipped with an Intel Core i5 processor capable of running AI- and WinCC-based SCADA and HMI solutions, executing other computing, monitoring, and controlling tasks — even on the go. To facilitate mobile utility, they weigh just 2.43lbs, have a large 10.1″ interactive screen and an 11.4V/3,500mA battery rated for six hours of use, and are available with accessories including a hand strap, shoulder strap, vehicle dock, and desk dock. To reliably withstand the various hazards common to industrial environments, they have few moving parts, IP65 sealing, and an extended standard warranty and are built and tested for military-grade durability.
These Industry 4.0 tablets also feature advanced Wi-Fi 6 and Bluetooth v5.3 mobile connectivity capabilities for efficient, uninterrupted data transmission and collection and optional RFID and barcode scanner modules for added value. They’re especially well-suited for facility and intralogistics applications with numerous frontline workers who may otherwise be less connected and can also be mounted in logistics equipment, like forklifts and stackers, to improve the speed, efficiency, and accuracy of picking operations and mitigate errors. This unique combination of features and capabilities allows users to remotely access, monitor, and control various systems, like production and assembly lines, in parallel and reduces the need for on-site visits, which — together — can help users reduce operating costs by up to 60%.
Sensors deployed in IIoT networks are essential to the digital transformation and robust integration of facilities and intralogistics operations. They digitalize and transmit critical equipment and process data, providing operators with valuable insights they can leverage to increase accuracy, boost efficiency, enable predictive maintenance and process optimization, reduce downtime, improve quality, and ensure regulatory compliance.
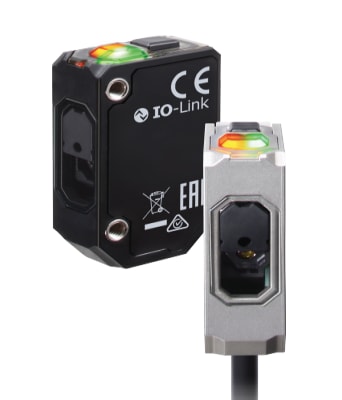
Omron Automation E3AS-F Series photoelectric laser sensors utilize time-of-flight technology to enable the indiscriminate detection of a wide variety of objects at the same sensing distance (50–1,500mm), regardless of target color, texture, contour, or sheen. This capability, combined with their small form factor, plastic and metal housing options, and environmental protections — including dust-tight IP67, waterproof IP69K, and oil-resistant IP67G sealing, Ecolab tested and certified for detergent resistance, and an anti-fouling coating on the lens — makes them well-suited for use in a variety of industrial environments, including wide-ranging conveyor applications in facility and logistics operations.
These sensors also offer IO-Link compatibility, which allows users to teach the sensor on the fly using a single button, as well as enable timer, continuous monitoring, and control output logic functions. One thing they’re especially well-suited for is replacing traditional encoders in automatic storage and retrieval system (AS/RS) applications in warehouse operations. These compact, non-contact sensors take up less space, don’t have a mechanical wear-out mechanism that requires frequent replacement, and are engineered for accurate sensing in even extremely dusty environments.
Motors and motor controls are important areas for consideration when trying to drive optimal productivity. AC drives, in particular, are essential devices designed to manually or automatically start or stop motors, facilitate their forward or reverse motion, regulate their speed and torque, and protect them against electrical failures. All motors have a controller of some type.
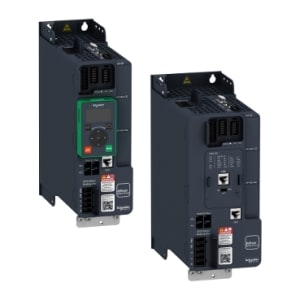
Schneider Electric Altivar Machine ATV340 Series variable speed drives (VSDs) are robust, IIoT-ready AC drives optimized for heavy-duty industrial applications rated for 0.75–75kW or 1–100Hp, including safe conveying, material handling, material working, and hoisting activities. They’re also especially well-suited for use in smart manufacturing facilities and dynamic applications with rapid acceleration. Their flexible design simplifies machine engineering processes with features including built-in multiprotocol capabilities (Ethernet, Modbus, and SERCOS), a variety of interfaces, an embedded encoder, integrated application functions, an embedded web server for remote monitoring and predictive maintenance capabilities, fast device replacement (FDR) capabilities that backup and restore its parameters, and compatibility with the company’s EcoStruxure Machine Expert Software, which allows users to configure and commission an entire range of elements in a single, user-friendly software environment.
Designed to improve the capabilities and availability of high-performance machines while reducing build costs, these VSDs offer a number of advantages:
- They provide superior machine performance with a maximum torque availability of 1.8ln, an optimized speed bandwidth of up to 400Hz, frequency inverters capable of handling high overloads in demanding applications up to 220% nominal torque, and high IGBT and thermal dissipation efficiency that allows for an additional 40% of rated current, taking motor power to 130kW under normal duty operation.
- Their fast application reaction times maximize machine throughput with a minimum 1ms task cycle and Ethernet connectivity.
- They reliably withstand harsh environments with high levels of dust and vibration and operating temperatures up to 60°C.
- They can shorten design cycles with complete project replication capabilities and one-button auto-tuning for motor identification.
- Their comprehensive functional safety and cybersecurity protections — including embedded STO (SIL3), SS1, SLS, SMS, SBC, and GDL — are compliant with machine-related safety standards EN ISO 13849-1 and EN 62061, and they have Achilles level 2 cyber-security certification to protect people and assets while ensuring service continuity.
- Their ready-to-use Tested, Validated, and Documented Architectures (TDVAs) and SoMachine software facilitate seamless automation integration.
Overcome Facility and Intralogistics Challenges With Industry 4.0 and RS
Whether you’re just starting to utilize Industry 4.0 solutions like IIoT devices in your facility management and intralogistics systems or are looking for ways to improve on the capabilities of your existing smart solutions, RS offers everything you need, including sensors, connectivity components, industrial data communications tools, PLCs and HMIs, and motor controls. The RS PRO line is also a good resource for curated, ready-to-go solutions, offering 80,000 high-quality products, including sensors, connectivity solutions, and industrial controls engineered to provide customers with an attractive combination of quality, choice, and value.
For more information about RS solutions optimized for facilities and intralogistics, please click the links embedded here. For assistance enacting or improving predictive and preventative electrical maintenance strategies or identifying, procuring, and deploying industrial MRO solutions optimized to increase process efficiency and productivity, reduce operational costs, and maximize equipment uptime, please contact your local RS representative at 1.866.433.5722 or reach out to our technical product support team.