Learn how Industry 4.0 technologies — including industrial data communications devices, motor controls, PLCs and HMIs, and specialized sensors, ranging from IO-Link devices to barcode readers — can help discrete manufacturers implement or enhance digital transformation strategies that improve quality, efficiency, and sustainability. These technologies also help overcome common challenges, including supply chain disruptions, leveraging legacy equipment, skilled labor shortages, and safety and security.
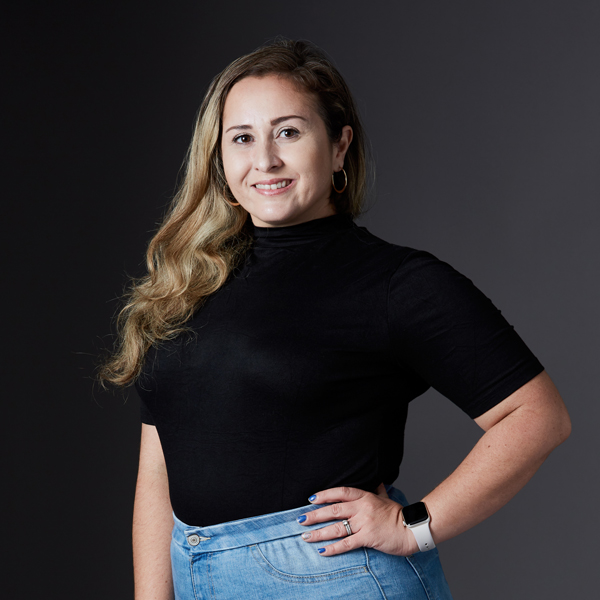
Discrete manufacturing operations generate countless products that individuals, businesses, and other entities rely on every day — everything from cars, electronics, and furniture to heavy equipment utilized in the construction, aerospace, and defense sectors. Discrete manufacturing involves assembling collections of individual parts or units of production to produce end products, and in recent years, this segment of the manufacturing industry has actively embraced digital technologies. A 2023 report by Eaton showed that, out of 133 respondents in the field, only 1% said they had no digital transformation strategy.
Technologies such as artificial intelligence (AI), the Industrial Internet of Things (IIoT), and cloud and edge computing — and the smart, connected devices that utilize them, including gateways, motor controls, PLCs, and sensors — are leading the way in Industry 4.0 and changing the way that manufacturers operate. The data that these technologies collect, transmit, and analyze can help manufacturers overcome common challenges and lead to better decision-making throughout their operations, ranging from better managing inventories to optimizing energy usage.
Many of the top challenges that discrete manufacturers face are ones felt by a broad range of industries, including supply chain disruptions, leveraging legacy equipment, skilled labor shortages, and safety and security concerns. In terms of core technologies, many of the solutions are also the same — squarely rooted in the latest technological and digital advancements — but are applied in unique ways.
Overcoming supply chain challenges with digitalization
Supply chain challenges are nothing new, particularly following the COVID-19 pandemic, where they were felt in acute, significant ways. But often, it isn’t a single point of failure within a supply chain that causes issues. There are many considerations, including varying consumer demand, component sourcing, transportation costs and disruptions, and lead times. These can be compounded in discrete manufacturing operations due to the sheer number of components — typically of a very specific type — needed to bring final products together. Digital technologies can help discrete manufacturers ease or prevent these issues.
Integrating smart devices, like IoT components, into industrial manufacturing systems and processes provides operators with more information than ever about the status of their various equipment and operations. When efficiently collected and analyzed, it also gives them valuable, actionable insights into the process, leading to better planning and decision-making.
Implementing machine and plant IIoT monitoring has the added effect of providing quicker insight into quality issues related to incoming raw materials and components, providing an opportunity to address supply chain issues,” according to Eaton’s Digital Transformation and Energy Transition report.
Automation also plays a large role in discrete manufacturing. Yet, as more devices are used to implement the latest technology, there is a greater need for flexibility in design through open machine controls. Machine controls allow operators to adjust the movement, speed, or sequence of various system components to improve precision, efficiency, quality, or safety, and open machine controls provide operators with an even greater range of options, including the ability to swap components out in the event of limited replacement part availability.
To ensure flexibility and compatibility among components, it is a good practice to select smart devices that utilize open hardware, software, or communications standards. These can include devices with Gigabit Ethernet, IEC 61131 compatibility, modern programming languages, or open standards-based industrial protocols, like OPC UA, Modbus TCP, IO-Link, and DNP3.
Industrial data communication devices, components that internally process system information, span from switches and routers to converters and gateways. Many are built with modularity and flexibility in mind to make it easier and more cost effective for users to grow and expand their system capabilities as the needs arise. For example, Ethernet switches that offer multiple ports allow operators to customize them to their specific needs. Additionally, many can support different communication protocols and networking speeds.
Banner Engineering’s Asset Monitoring Gateways (AMGs) with SNAP ID, for instance, are designed to help manufactures think big, start small, and scale fast. Designed to collect and analyze data from up to 20 connected sensors, Banner’s AMGs with SNAP ID help users make important decisions that can help increase productivity, save energy, and prevent unexpected maintenance issues. They also feature a user-friendly, no-code setup and are preconfigured to automatically recognize a wide variety of compatible wired sensors right out of the box, allowing users to get up and running in minutes versus months.
Compatible sensors are available in discrete, analog, and IO-Link variants — made by both Banner and other suppliers — and are designed to measure variables including vibration, differential pressure, temperature and humidity, and tank level in applications including conveyor systems, industrial fans, pumps, electric motors, compressed air systems, and dust collection units. AMGs with SNAP ID also feature an onboard touchscreen display and compatibility with Banner’s Cloud Data Services (CDS) platform.
Connecting the AWG to Banner CDS using Ethernet or cellular connectivity provides users with access to their data in customizable online dashboards designed to give maintenance and production teams real-time visibility into actionable equipment data essential for identifying trends, optimizing performance, predicting maintenance requirements, avoiding costly equipment failures, and preventing unplanned downtime.
Banner Engineering also offers AMGs with CLOUD ID. These rugged, IP67 industrial data communications devices make it easy to add wireless condition monitoring capabilities to equipment located anywhere in or around an industrial facility, and — just like the AMGs with SNAP ID — are designed to get users up and running fast. Banner’s AMGs with CLOUD ID also automatically detect every compatible sensor or node that’s paired with the IIoT gateway, and, unlike the AMGs with SNAP ID, they can connect up to 200 compatible devices. Additional benefits include the ability to transform data at the edge using the integrated DXM configuration tool or further customize it with ScriptBasic or MicroPython.
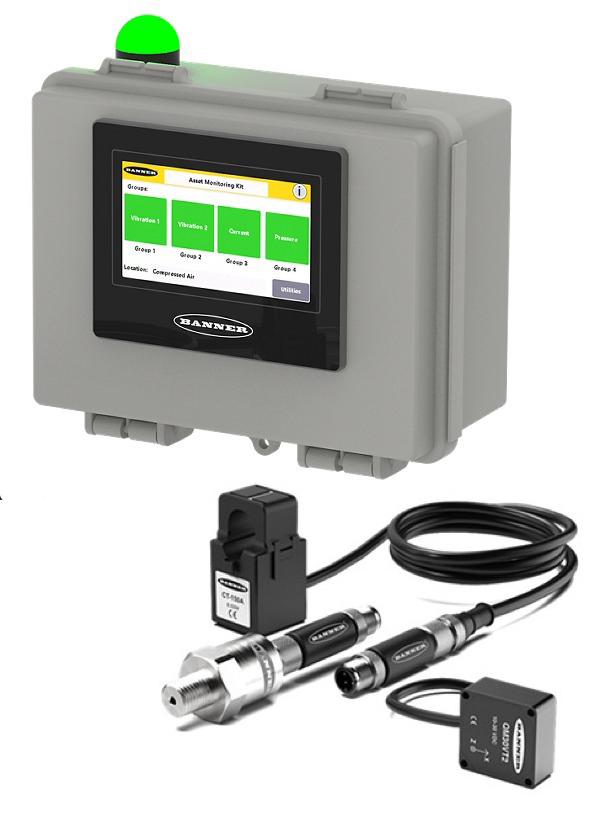

Due to their quick, easy, and intuitive code- and programming-free commissioning, users don’t need to hire or involve specialized systems integrators to implement these smart gateways or expand upon the number of devices they monitor, saving them both time and money and making modularity and scalability a breeze. Additionally, Banner’s compatible VIBE-IQ software uses machine learning (ML) to automatically set and monitor vibration thresholds for rotating assets, making it easy for non-experts to spot issues early and better maintain equipment without any complicated analytical work.
Overcoming legacy equipment challenges with digitalization
While the benefits of digitalization technologies are undeniable, the speed of advancements can cause machinery to become outdated or obsolete quicker than ever.
According to Eaton’s Digital Transformation and Energy Transition report, “Innovations in robotics and manufacturing machine capabilities have dated even relatively new plants. For example, an early computer numerical control (CNC) industrial robot now competes with more flexible models that have computer vision, AI processing, and IIoT connectivity, performing a wider range of tasks.”
To keep pace with changes, it’s critically important that manufacturers invest in information technology (IT) and operational technology (OT) infrastructure built with updates in mind. This is another reason why utilizing open-source and flexible hardware, software, and communications can benefit businesses. Working with equipment suppliers offering a broad range of products designed for modularity and featuring flexible component solutions can also allow you to scale as needed. Manufacturing execution systems (MES) can aid in managing and optimizing increasingly complex and multifunctional manufacturing process as well. But the success of these systems relies on implementing the right tools.
“MES’s capabilities align well with these sectors’ demand for quality control, traceability, and compliance,” according to a MarketsandMarkets report about MES in the process and discrete manufacturing industries. “Implementation of generative artificial intelligence, digital twin, and edge computing are some of the critical trends that are expected to drive the ecosystem of the MES market in the next 5–6 years down the line.”
Edge computing — where data processing occurs close to the sources rather than in a central location, such as an external data center or the cloud — can help bridge the gap between older and newer equipment by accepting a wide range of inputs, even if a component is decades old. With numerous connectivity protocols available, devices often struggle to communicate with each other. The right edge computing devices can act as translators in addition to offering advanced features like networking and firewall functionality. As such, they are rapidly growing in popularity. Organizations in the logistics and transportation industries, for instance, are using them to improve real-time tracking, autonomous forklifts, and fleet management operations.
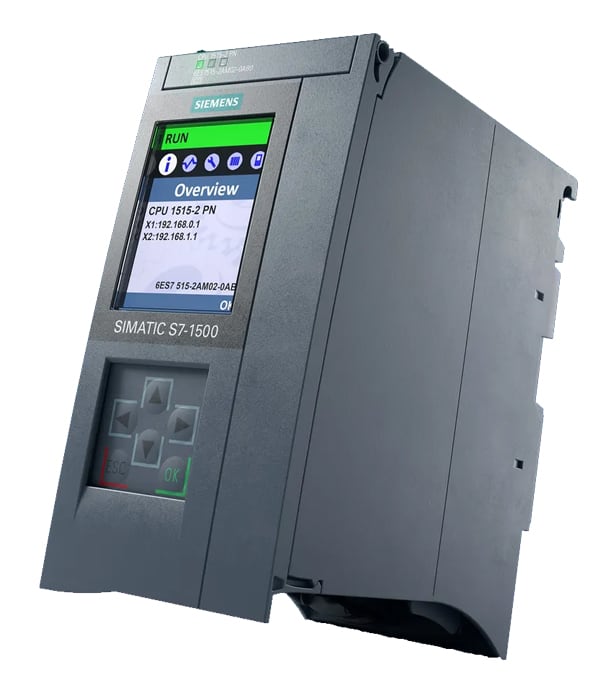
The Siemens SIMATIC S7-1500 controller features a modular, fully scalable design that’s engineered to help users implement today’s advanced digitalization technologies, like edge computing and AI, while simultaneously providing them with a clear path for continued digital transformation.
Central processing units (CPUs) are the heart of the SIMATIC S7-1500 PLC. These components execute user programs, network the controller with other automation components, and improve productivity and efficiency.
Digital and analog signal modules, or peripheral modules, form the interface between the controller and the process to support scalability, performance, and usability. The controllers leverage connected sensor data to record the current process status and trigger corresponding actuator reactions, while the signal modules provide the exact inputs and outputs required for the task at hand.
Specialized technology modules (TMs) leverage the intuitive parameterization and efficient programming capabilities of the Siemens Totally Integrated Automation (TIA) Portal to enable signal preprocessing close to the hardware for extremely fast counting and measuring, as well as precise position detection for incremental and Synchronous Serial Interface (SSI) absolute encoders. They also feature various process alarms to support fast reactions to internal and external incidents and counter values and — like the SIMATIC S7-1500 signal modules — can be used both centrally (i.e., directly at the SIMATIC S7-1500 CPU) and decentrally in the SIMATIC ET 200MP I/O system.
One technology module, the TM MFP, features an open design customized for high-level language applications (e.g., C/C++) to enable the integration of edge computing, protocol converters, database connections, complex algorithms, and vision systems. Another model, the TM NPU, uses a trained neural system to enable simple, profitable combinations of AI algorithms and PLC logic.
Lastly, communication modules offer additional functions and interfaces designed to further increase the flexibility and performance of automation systems utilizing modular SIMATIC S7-1500 controllers and/or modular SIMATIC ET 200MP I/O systems. The SIMATIC S7-1500 CPUs feature integrated PROFINET and PROFIBUS DP communication interfaces. These additional interfaces enable the realization of complex automation structures and process optimization via connections with enterprise management equipment.
Overcoming labor challenges with digitalization
With an evolving industry comes a changing workforce. These employees may be well-versed in high-level programming languages, such as such as C/C++ and Python, and newer technologies. However, with such a wide variety of platforms available, even well-educated workers’ skills and knowledge may not fully align with manufacturers’ needs.
In addition, industrial firms continue to face skilled labor shortages.
“Manufacturing industries face increasing competition for scarce science, technology, engineering and math (STEM) resources, and decreasing interest and time available for engineers to learn at a hands-on level as previous generations did,” according to an EY article about digital strategies for the future of manufacturing.
One way to help overcome this challenge is to utilize products designed to enable quick, easy, and intuitive installation and low-code or no-code plug-and-play commissioning in new and existing industrial systems, like Banner Engineering’s Asset Monitoring Gateways (described and pictured above), Red Lion Control’s N-Tron NT24k Gigabit managed Industrial Ethernet switches (below left), and RS PRO’s SW-615RS five-port Gigabit-hardened Ethernet switch (below right).

Other times, devices can be combined to create an all-in-one solution that reduces or eliminates manual labor requirements. For example, asset monitoring gateways compatible with IO-Link sensors, like Banner’s, are multipurpose solutions that enable businesses to access useful data quickly and easily while connecting components through other communication technologies, like Narrowband-Internet of Things (NB-IoT) for low-power, wide-area (LPWA) applications.
These IIoT solutions provide real-time information and data about system performance, eliminating the need to manually monitor machinery, reducing the impact of skilled labor shortages, and freeing employees up for higher-level tasks. This also helps manufacturers avoid unplanned downtime and subsequent supply chain disruptions by identifying urgent and impending maintenance requirements, optimize maintenance schedules to minimize the impact of taking machines offline, and even troubleshoot issues.
Digital interfaces can help manufacturers ensure equipment is accessible to employees with various skill levels. Human-machine interfaces (HMIs) feature visual displays designed to be easy to read, understand, and engage with and touchscreens and keypads designed to enable precise controls and inputs and reduce the risk of miscalculations and oversights.
Automation can also help alleviate labor shortages by taking on more repetitive tasks, allowing employers to utilize skilled workers for more complex tasks. For example, AI applications can power tasks when paired with programmable logic controllers (PLCs) programmed to respond based on inputs from other devices, like sensors, and smart motor control solutions can automatically monitor and optimize the performance of connected machinery.
The TeSys island digital load management system from Schneider Electric is one such solution. The TeSys island solution consists of a set of devices — including couplers, analog and digital I/O modules, voltage and power interface modules, standard motor starters, and SIL motor starters — installed on a single DIN rail, connected with a ribbon cable, seen as a single node on users’ networks, and engineered to improve the installation, availability, safety, operation, and service life of electrical controls in a wide variety of automation architectures, primarily via the direct control and management of low-voltage loads.
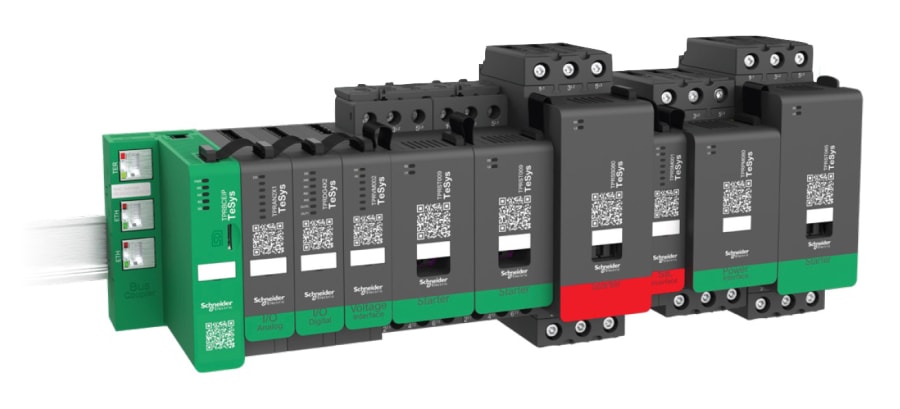
This modular, multifunctional, plug-and-play system also empowers users to remotely monitor and control motors and other loads through a secure digital platform, which can help reduce the impact of labor shortages and minimize on-site staff deployments, as well as enable users to employ predictive maintenance strategies that can help prevent unplanned downtime, optimize the scheduling of planned downtime, troubleshoot issues quickly and accurately, and improve equipment uptime, efficiency, and lifespans.
Another way Schneider Electric’s TeSys island digital load management system helps reduce the impact of labor shortages and costs is through ease of use. Its simple, modular, click-together device design eliminates control wiring and mechanical adjustments, minimizes breakage points, and enables quick, easy, and cost-effective installation. The intuitive and user-friendly software allows users to select and modify prebuilt digital functions instead of writing code line-by-line, which makes configuration and programming a breeze. Its compatibility with third-party PLC and automation platforms, including Schneider’s powerful EcoStruxure platform, Rockwell Studio 5000, and the Siemens TIA portal, simplifies and speeds integration and commissioning as well.
TeSys island is designed to manage motors and other electrical loads up to 80A (AC1) or 40hp, 480V, and 66A (AC3) and supports up to 20 modules connected to one bus coupler under a single 24V supply. It also supports EtherNet/IP, Modbus TCP, PROFINET, and PROFIBUS fieldbuses and features integrated digital and analog I/O that eliminate the need for distributed I/O. Additional features include Achilles Level 2 cybersecurity certifications and PLe Cat4, SIL 3, and SIL CL3 functional safety certifications.
Overcoming safety and security challenges with digitalization
No industry or business is immune to the threats of cybersecurity. While IoT devices provide numerous benefits — including vast amounts of system, equipment, and process data that enables better decision-making and real-time insights into urgent and impending performance issues — being connected to the internet comes with inherent risks. And for those who use open software, the stakes are even higher.
As such, it’s imperative that manufacturers incorporate adequate protections into every level of their automation platforms. Utilizing smart devices, equipment, and parts equipped with integrated security features is key. Many internet-connected devices, like IoT edge gateways, offer security features like firewalls and VPN protection.
In addition to cyber concerns, physical safety is a top priority in industrial manufacturing environments. Connected devices with condition monitoring and automation capabilities, including PLCs, sensors, and smart motor controls, like Schneider Electric’s TeSys island, can help detect, relay information about, and respond to equipment problems in real time, ensuring an operator- and equipment-safe work environment while simultaneously improving product quality, process efficiency, sustainability.
Another key safety concern in discrete manufacturing environments relates to finished products that have come off the production line and entered the market. Traceability plays a vital role in discrete manufacturing — especially within the automotive, aerospace, defense, and medical electronics industries — providing supply chain partners and regulatory agencies with a way to identify source information, such as serial number, manufacturer, and production date, for each component part of the end product. Traceability provides transparency and accountability throughout the supply chain, protects manufacturers and consumers from counterfeit products and supply chain partners from errant liability claims, facilitates product recalls, improves production processes, product quality, and safety measures, reduces waste, and facilitates compliance with regulatory standards.
Precise markings, like barcodes, play a critical role in traceability. Often, industrial barcodes and their readers — yet another key industrial sensor technology — need to be robust enough to withstand the various hazards of harsh industrial manufacturing environments, including exposure to high heat and chemicals.
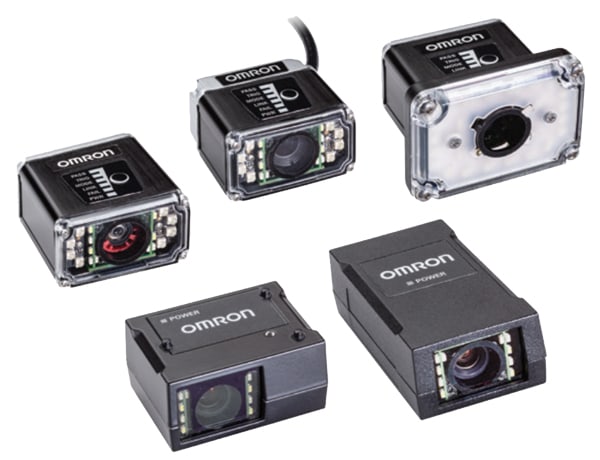
Omron Automation offers a number of traceability solutions engineered for exactly this. Its MicroHAWK barcode reader family, for instance, features ruggedized and extremely compact IP67 form factors equipped with the smallest, highest-performing imaging engine in its class and optimized for flexibility and usability. These devices can be used as both barcode readers and visual inspection systems. As such, they’re widely used for regulatory compliance, process automation, quality assurance, inventory optimization, and serialization in applications extending throughout the discrete and process manufacturing industries, ranging from the automotive, consumer electronics, and industrial equipment segments to the food, beverage, and pharmaceutical manufacturing segments.
MicroHAWK industrial barcode readers support Ethernet and PoE connectivity for broad compatibility with control hardware and daisy chain configurations that minimize cabling requirements, reduce cost and complexity, and simplify device management and system scalability. They also feature an intuitive, web-based setup and control interface, WebLink, that democratizes installation, commissioning, and condition monitoring processes — the latter of which provides users with actionable data about overall equipment effectiveness and facilitates process optimization. Other advantages of the MicroHAWK range include options with auto-focus lenses up to 5MP resolution, advanced X-Mode decoding algorithms that allow users to accurately identify damaged barcodes, and integrated LED lighting with high-intensity ring light.
Tackle your digital transformation strategy with the right technology partner
Whether your business is early in its digital transformation strategy or looking for ways to scale and improve an already established system, it can be a complex and multifaceted process. While discrete manufacturers face many common, industry-wide challenges — ranging from supply chain disruptions and legacy equipment to skilled labor shortages and safety and security — and even utilize many of the same core technologies used to surmount these issues in other industrial market segments, the successful selection and deployment of these technologies is often tailored to unique operating environments and application demands. Navigating these intricacies can be its own challenge, but it’s not insurmountable, especially with the right resources and technology partners.
To learn more about Industry 4.0 digitalization technologies and the RS portfolio of discrete manufacturing solutions, including industrial data communications devices, motor controls, PLCs and HMIs, and specialized sensors, ranging from IO-Link sensors to barcode readers, please visit the links embedded throughout this article. To begin or enhance your digital transformation and integration process, please contact your local RS representative at 1.866.433.5722 or reach out to our technical product support team.