Jeff Thornton, Product Manager, Red Lion Controls
RS’s “Ask The Expert” series taps into the experience and expertise of key thought leaders and subject matter experts from the more than 550 global suppliers we work closely with to bring customers solutions for their most challenging problems (and the daily ones, too).
In this edition, we talk with Jeff Thornton, product manager for Red Lion Controls, about smart panel meters and their graphics displays. Jeff explains the different ways machine operators use the data from the meter’s connectivity and additional screens for better performance on the factory floor, faster responsiveness to production or equipment issues, and time and cost savings.
How can a connected or “smart” panel meter make a factory smarter and perform better?
Panel meters are a universal item. They’re used in the factory floor, food and beverage, water/wastewater, and packaging, just to name a few. A panel meter’s function is to provide the machine operator with a data point, such as a count value, temperature value, pressure value or another measure. In today’s connected world, these data points gathered together can provide useful information to drive scheduling actions or process improvements. Moving from a numeric display to graphics provides the operator with a more intuitive display. Think of the gas gauge in your car—one simple glance and you know exactly what you need to do. Now, machine operators can share a similar experience and apply it to production on the factory floor.
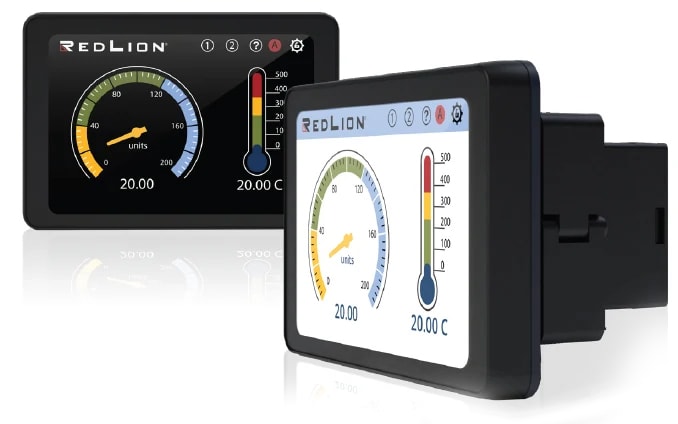
In your new PM-50 brochure, you also mentioned that you can see more than just information; you know what the information means and react to it quicker. Can you give us more detail on this?
The graphics display helps the operator understand what the data means more quickly, enabling them to make faster decisions that affect efficiency, workflow and even maintenance. Additional screens with the smart panel meter provide them with more data to be better connected to their machine and job requirements. For example, a typical application is measuring flow. With the additional screens, the operator can measure flow in a pipe while also controlling the level in the tank on a different screen. Previously, this would require two meters for this application. A smart meter allows machine operators to be more efficient and act on the data points right away, if necessary, and get a bigger picture of how their factory is performing in real time.
Smart device connectivity also allows the operator more freedom to move around and monitor additional equipment while still staying connected to their machine. An app allows this monitoring and provides alarm indication when the machine is not running correctly or the job is completed. Adding additional equipment, like an HMI (human-machine interface) or another device would allow a single operator to manage a bank of machines, reducing the labor footprint and increasing the efficacy of the operator.
Serviceability is key on a factory floor. How are installation and upgrades made easy
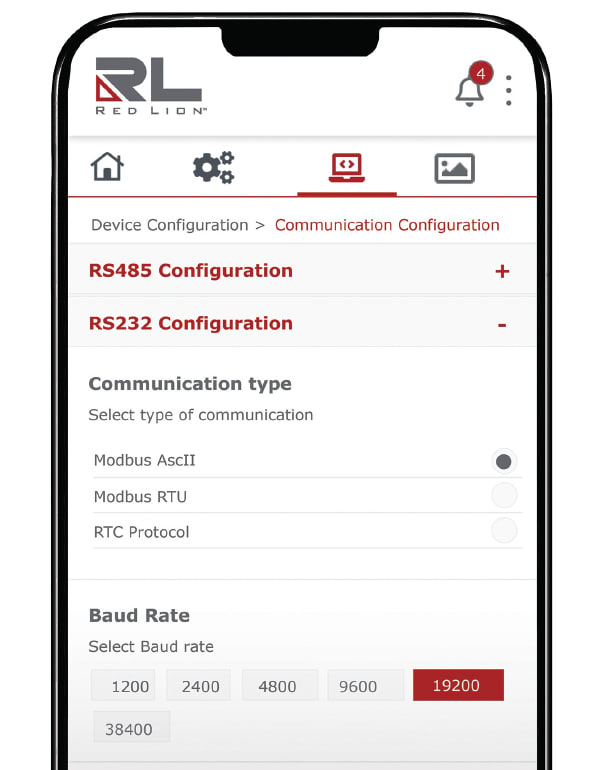
Red Lion’s new PM-50 meter looks and feels like other smart devices, including the programming, so making changes and trouble-shooting is very easy. The workforce today is more familiar with smart devices, in general, and therefore more comfortable using them and getting as much information as they can out of them. A new feature on the PM-50 is the ability to update the firmware of the panel meter using the SD card or web browser. This enables new features or functions released over time to be added easily to the current meter if needed for the application.
How does a smart panel meter improve performance and drive down costs at the same time?
The real issue is getting existing stranded meters connected so their data can be harvested. The cost to add communications to a meter and then run wiring to connect the meter can make the whole effort too expensive—in time and money. Estimate two to three hours for the system maintenance person to run wiring from the collection point to the meter location. If you have 20 meters to connect, it will take 40 hours or more to get the data. Maintenance has too many pressing issues to spend that amount of time to run wires and enable you to get the data. In addition to time, there are labor costs and equipment costs for the cabling and connectors.
Using the PM-50 and its Wi-Fi communication completely eliminates costly cable runs. With this wireless smart meter, you can access all the data on the plant floor and get an overall picture of your plant’s operations to make improvements or adjustments in real time, as needed.
How does a smart panel meter, particularly the PM-50, allow manufacturers and plant managers to create a “smart” workspace, connecting even older technology together in a simple way?
Today’s plant floors likely have some newer equipment that provides some communication. However, the panel meters are usually stranded machinery. The PM-50 can enable these data points to be extracted from older equipment to provide a complete plant floor overview. The graphic displays improve the operator’s experience, making them more productive, while the data gives management a better understanding of product flow through the plant. Even properly running older equipment is a vital part of the plant floor, so bringing in the data from those machines helps complete the plant floor picture to make even better decisions. The smart panel meter benefits OEM machine builders, as well, because the product provides their equipment with a better appearance and wireless communication, which represents a huge advantage for both the OEM and their customers.
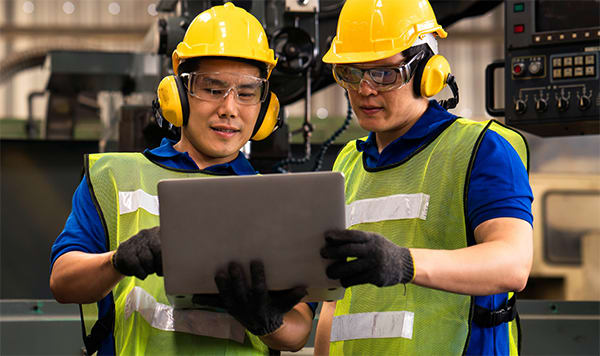