RS Ask the Expert: How Can Manufacturers Rapidly Face and Conquer Supply Chain Challenges in the Wake of a Worldwide Pandemic?
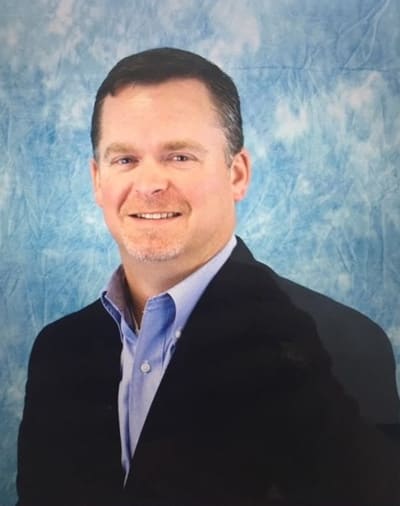
Ty Golden
Director of Supply Chain Planning, RS Electronics
RS’s “Ask The Expert” series taps into the experience and expertise of key thought leaders and subject matter experts from the more than 500 global suppliers we work closely with to bring customers solutions for their most challenging problems (and the daily ones, too).
In this edition, we talk with Ty Golden from RS Electronics, director of supply chain planning in Fort Worth, Texas to understand the ripple effects a worldwide pandemic caused in the production of goods. It has presented a great challenge to the supply chain pipeline that equips not only maintenance, repair, and operating (MRO) supplies,
but direct material as well.
It seems U.S. manufacturers are in a COVID conundrum: while many manufacturers were down hard when the coronavirus first hit, demand for many categories of goods then surged. This presented a real problem of limited supply. Recently the Wall Street Journal reported that “Many manufacturers continue to suffer from inventory shortages, a remnant from when plants were closed last spring.” From your perspective is this something to be concerned about or is it a temporary kink in the flow of goods?
There was an initial impact to global manufacturing and distribution due to uncertainties from COVID-19 – related to the supply and demand of goods. After a very brief period of pause, an urgent surge occurred in manufacturing demand for products used to mitigate and combat the effects and prevention of the virus, including medical and healthcare, pharmaceutical, PPE products, ventilation equipment and parts, thermal temperature scanning solutions, and other related products. A shift in priorities and resources within manufacturing happened with an intent to build up the supply and to produce such goods to meet a newfound, unprecedented demand.
Reactive supply and demand cycles pose challenges within supply chain networks. While they cause concern, it drives a strategy for manufacturers and distributors to better prepare for supply and demand swings within the markets they serve. In many cases, it’s not a matter of if, but when such swings will occur, and the degree of such impact.
While it may be a temporary kink in the flow of goods, it takes time to re-establish stability across the entire end-to-end supply chain network.
You can think of it like an accident on a major highway. It only takes minutes for the accident to occur, but hours for the traffic to start flowing at its normal pace again. During the time the accident on the major highway is worked by local law enforcement, EMT, tow trucks, and all responders; feeder exits, access roads, side streets and alternate routes become overwhelmed with vehicles. The demand immediately exceeds the supply of available roads. The effect becomes a bottleneck. The supply chain essentially experienced a bottleneck in global manufacturing at the beginning of the pandemic.
One manufacturer mentioned how if the supply of something as small and seemingly incidental as a container cap is thwarted, it could put them out of business. No matter how small the part, a lack of supply can be the critical path to operational flow and productivity. Can you comment on this? Ever see situations where a breakdown – even in a small part of the supply chain – caused detrimental effects?
It may be difficult to imagine how a small or incidental commodity or component part could have such a significant impact to a major manufacturing project, but it happens. With 20-plus years of experience in the distribution of mechanical and electrical components, I’ve seen such products occasionally thwart or stall multi-million-dollar projects.
Breakdowns in supply chains happen. Preparation, agility, and prompt reactions by all supply chain stakeholders is key. It also highlights the importance of business continuity planning (BCP) within an organization to be well prepared with a disciplined approach for managing supply chain breakdowns.
Equally important is the maintenance of strong and healthy relationships with business partnerships, customers, suppliers, and employees, as such alliances play a major role in collaborating smartly during times of crisis and urgency.
What’s your advice to avoid shocks to the supply chain? Is it all about planning? Contingency planning with alternatives? Knowing when to stockpile?
There are a variety of methodologies, tools, technology and resources to help mitigate supply chain risk, and avoid major disruptions in supply chains.
Inventory policy settings within your business’s planning applications help mitigate variability in the supply chain; however, it should not be the only means of protection. Considerations for inventory protection strategies within your business are very useful, if executed appropriately in today’s digital business environment of web services and on-line order processing.
Knowing when to stockpile, and more importantly, how to manage the distribution of products and solutions across all the demand requirements on the business is crucial.
What are some best practices for purchasing and procurement professionals to embrace, given the risk of uncertainty at any time?
Robust inventory planning solutions and technologies are critical. The use of a strong digital fabric of tools, technologies and platforms, fully integrated with legacy ERP systems, is a smart and necessary business practice.
Inventory planning solutions enable for automated processes related to demand planning, forecasting, supply planning, sourcing, purchasing, delivery and exceptions management, and several other related functions.
Don’t shy away from technology and automation. Embrace current technology and leverage the available analytics provided. Don’t stop asking the questions: What’s next? What could it be?
Supply chains don’t live in the present. They learn from the past, and they should always be planning for the future.
How can a distributor help curtail risk in a manufacturer’s supply chain?
A robust distribution model provides a multitude of valuable solutions for manufacturers. These include solutions related to marketing, sales, customer acquisition, new product introduction, inventory management and supply chain solutions for the markets they serve.
This allows manufacturers to focus on their core business model- the production of goods, while strategically partnering with distribution to manage the ever-changing supply and demand requirements of a broad and variable customer base.
When managed properly with healthy and strategic business partnerships, a distributor is very valuable. The distributor helps curtail risk in a manufacturer’s supply chain with strong and proven inventory management and supply chain solutions. Such solutions provide confidence in the end-to-end processes for fulfilling customer’s requirements.
A distributor, with the right solutions and capabilities, brings new customer opportunities to all manufacturer business partners’ sales and marketing channels via their digital presence. A distributor’s investment in inventory management and supply chain solutions boosts a manufacturer’s competitiveness within the volatile and challenging supply chain environment which currently exists.
Additional Links: