We spoke with Stephen Berestecky of ebm-papst to learn more about compact fans, which are an essential component of thermal management solutions in industrial and commercial electronics applications.
Stephen Berestecky, Director of Business Development and Market Manager, ebm-papst
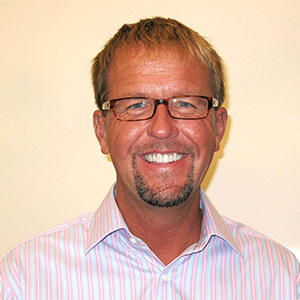
Electronic components must be consistently and effectively protected from environmental factors that pose a threat to safe and error-free operation, including temperature extremes. Temperature is a key variable that industrial and lighting engineers must consider when selecting components and drafting their designs. Heat is the enemy of most electronic components, devices, and systems, so there are a variety of different thermal management tools and technologies designed to help keep electronic products within their rated operating temperature range, including fans, heat sinks, thermoelectric coolers, forced air systems, and heat pipes. Due to the combined demands of the electronification and space optimization trends, compact fans are one of the most common electronics cooling solutions. These devices play a vital role in keeping applications including data servers, telecom systems, lighting systems, and machines running safety and effectively.
To learn more about electronics cooling and compact fans, we spoke with Stephen Berestecky, the Director of Business Development and the Market Manager for IT / Telecom, lighting, and digital signage at ebm-papst. The company is a leading global supplier of ventilation and drive technologies engineered to provide efficient, intelligent solutions for commercial and industrial applications in the factory automation, lighting, digital signage, appliances, HVAC, commercial refrigeration, agriculture, and automotive industries, just to name a few.
Hi Stephen. Please tell us a little bit about yourself. How did you come to work at ebm-papst, how long have you been there, and what do you do in your current role?
I am the Market Manager for our IT / Telecom, lighting, and digital signage business, and I serve as a resource for our field sales organization to help better serve our customers. I’ve been with ebm-papst for 15 years but have actually known them as a customer and collaborator for at least 15 years before that. As a thermal engineer who designed cooling architectures for computers and other electronics cooling applications, and someone who qualified fan suppliers for a telecom company, I got to know ebm-papst and their products very well and formed terrific relationships with many people on both the U.S. and German R&D teams there. After my telecom career ended, I started my own company to help clients with thermal design and testing. When my partners and I sold our company, ebm-papst asked me to join the team, and I said yes instantly because I was so familiar and impressed with their products, expertise, and company culture.
Why is electronics cooling so crucial?
Heat is the enemy of most electronics, but most of the electrical power drawn by electronic devices and equipment is dissipated as heat. As such, most electronic systems tend to run much warmer than room temperature. This fact proves especially problematic in today’s compact and densely packed electronics designs, which don’t leave much room for airflow and cooling devices. Components like computer chips experience thermal dissipation, or wasted power, as temperatures increase, and others, including solid-state electronics, can break down and fail. Effective electronics cooling designs lead to longer product lifetimes and enhanced reliability, and given the increasing power densities of just about everything, the need for thermal management keeps growing.
For instance, a major operating concern for any given data center is how much power it consumes. 35–40% of the energy dissipated in a data center comes just from turning fans and blowers, but that cooling is vital to the center’s operation. For data centers and telecommunications systems, the number one rule is that failure isn’t an option. So, in order to ensure effective operation and long equipment lifetimes, these applications must be designed to maintain the optimal air temperature throughout the systems.
Digital signage is also becoming more dynamic, leveraging data to give you up-to-date information that’s tailored to your needs. An example is airport baggage claim signs that indicate the wait time for baggage from arriving flights. Digital signage also includes larger displays like the screens in Times Square or the Oculus video display at SoFi Stadium in L.A.

The Oculus video display is the most expensive sports screen ever built and has the highest technology LED arrays ever used to date. To protect that investment and ensure its safe and effective operation, it has 7,500 of our RG160-28/14NU blowers in it.
What are some of the most common challenges designers face when implementing thermal management solutions?
Digital signage and LED lighting have similar thermal management challenges. Scoreboards, for instance, often use panels of LED arrays that sit in tile arrays measuring approximately one or two square feet. All of the LEDs in each tile must all run at the same temperature, or the color of the LEDs will change and distort the on-screen image.
Standards exist to help us overcome these challenges. For example, the reason why telecommunications systems always work (provided that there’s power) is that all of the critical components and devices must follow the same specific standards, like the Networking Equipment Building Specification (NEBS) GR-63. This standard, which views air movers as components, is very specific in terms of how computer equipment and other office devices need to be maintained from a thermal management perspective, and it mandates the redundancies that must be built in to prevent downtime if a component fails. Standards like these add to the challenge for thermal engineers, but there are tricks of the trade that help them work around that, like utilizing N+1 designs.
N+1 system designs are constructed so that if one component (N) fails, the others take over and make up the difference. For example, if you have a telecom system with 20 fans within the cooling chimney or the cabinet — 10 fans pushing and 10 fans pulling — and one of those fans fails, the other 19 fans will react in a way that maintains the cooling capabilities of the fully operational system. However, there may not be any air directed at the electronics closest to the failed fan anymore, which could still cause issues if not addressed quickly enough. So, thermal engineers working with critical applications like telecom system and data centers tend to build in countermeasures or redundancies including speed control, diverters that redirect air, and shutters that prevent backflow to ensure there’s no downtime.
Are fans the only go-to solution for thermal management or just one of the most popular, and if so, why is that?
Fans are definitely among the most commonly used thermal management devices in the IT / Telecom, medical, alternative energy, transportation, lighting, and digital signage industries. Blowers are also commonly used, but are usually reserved for larger scale applications, such as the Oculus video display I mentioned, data centers, and agricultural and industrial systems.
The reason fans are often more ideal is because of a concept called zoning combined with N+1 system designs. When you have a blower fail in a system, it can be a nightmare to try to get the other air movers to make up the difference and recover from the failure. So, many industries have figured out that it’s smarter to populate a chassis with even extensive arrays of fans than with fewer blowers. When you lose one, it’s much easier to detect a hot spot, identify the failure zone, and speed up the failed fan’s neighbors to compensate for the loss than to try to get other air movers to make up the difference of losing a powerful blower because you have so many more of the same size fans nearby.
Can you provide us with a brief introduction to compact fans and the types of markets and applications they’re used in?
Compact fans can be anywhere from 25mm to 280mm in diameter and can be used in virtually any application where effective thermal management is critical to reliable operation. Common market segments include IT / Telecom, lighting, digital signage medical, alternative energy, agriculture, factory automation / control, and appliances. Typical applications include control cabinets and enclosures, power modules in 5G network infrastructure, variable frequency drives, streaming servers, data centers, automation equipment, digital signage, and LED displays — virtually all of which are subject to installation space constraints and, as such, present cooling challenges.
Axial, diagonal, and centrifugal fans are three of the most common types of compact fans.

Axial fans are suitable for applications with high air flow and medium pressure increase, like heat exchangers. They are typically equipped with an external housing, and the air flows through the fan blades parallel to the axis of rotation, or axially. Desirable characteristics include a minimal installation depth, low noise level, and exceptional efficiency. ebm-papst manufactures a wide range of extremely shallow-depth, low-noise, and high-efficiency 25 to 280mm AC and DC fans with the motors integrated into the fan hub for additional space savings. We also manufacture a large Hyblade axial fan for large-scale applications like HVAC systems.

Diagonal fans are similar to axial fans in that the air is drawn in axially, but the outflow is diagonal. The conical shape of the impeller and housing results in greater compression of the intake air, so diagonal fans are better for high-airflow, high-pressure applications with intensive cooling requirements, like control cabinets with high component counts, and can withstand higher backpressure caused by clogged filters or higher power density. They also exhibit lower operating noise levels at high pressures compared to the same size axial fans with similar performance specifications.

Centrifugal fans, which ebm-papst also refers to as FlatPak blowers, are ideal for ultra-high-pressure applications. Ours feature 90° air deflection and aerodynamically optimized impellers and are available with forward- or backward-curved blades and in many sizes and configurations. They are also compatible with extremely compact 1U and 2U rack-mount servers, are relatively quiet given their high-pressure capabilities, and can be used in applications including medical equipment, data centers, and appliances.
What are the primary factors that customers should consider when selecting a compact fan? Are there any must-have physical or electrical characteristics?
Optimal fan characteristics depend on the application at hand. In order for suppliers to help a customer select the right fans or design the right cooling architecture, we need to know the operating point to determine how much airflow is needed at a given backpressure. Other vital variables include how much power will be delivered to the fans and the impedance of the system, or its resistance to air passing through. At ebm-papst, we have state-of-the-art, industry-certified test labs where we can test airflow and impedance for equipment ranging from computers to rooftop air handlers and even vehicles. Once we know the impedance of a given application, we can select the ideal fan size with the optimal power, noise signature, and overall performance characteristics, including desired lifetime, space constraints, intelligent networking needs, and energy efficiency targets.
Modularity can allow for application-specific customization, even in unusual deployment areas and challenging environmental conditions. Ingress protection (IP) is often a critical design feature as well, especially in high-moisture and high-particle environments. In general, the higher the IP rating required, the higher the cost of the air mover selected. But knowing that your fan is well suited for the operating environment is vital, so the cost is worth it.
It’s important to note that 99% of failures in the field are caused by the bearing system in the fan wearing out. This is why ebm-papst developed proprietary formulas for ball bearing grease that’s specially formulated for certain types of applications and environments. Options include a grease that’s suitable for controlled environments like Central Offices, greases made for use in extreme cold and extreme heat, and greases made for combination environments. Our attention to this key component of fans is a big reason why our company is known for product reliability, and it’s certainly a key part of design that engineers need to focus on.
In fact, the entire ventilation system should be looked at as a whole. Sourcing all of your solutions, or as many as possible, from a single supplier can ensure that the components are perfectly matched and can also help you leverage opportunities for digitization at an early stage. Working closely with a single supplier can also give you access to services like acoustical octave band analyses. Humans are sensitive to certain frequencies of acoustic noise, and experienced suppliers can help manage audible sounds by identifying the best way to mount a fan or blower to minimize annoying frequencies associated with structure-borne noise.
Does ebm-papst offer any particularly effective and efficient compact fans that potential customers should consider? If so, how do these solutions compare to compact fans from other leading suppliers?
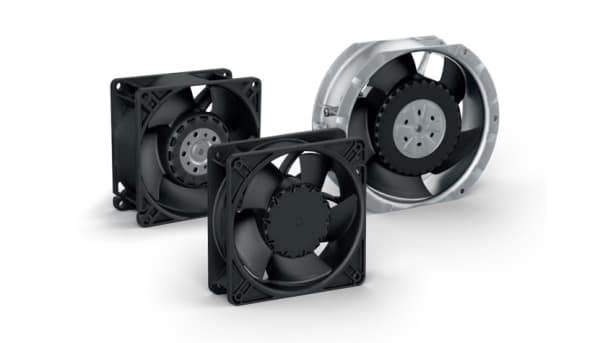
Our specialized ball bearing grease formulas are just one of our many competitive advantages. Our motor technology sets standards for sophisticated electronics and aerodynamic designs, and we offer fans that combine the highest available energy efficiency with the added benefit of IoT and digital networking.
Our AxiForce series of tubeaxial compact fans is a great example. This product family has a steep air performance curve for maximum efficiency, an acoustic noise advantage of up to 6dB(A), salt spray protection, and ingress protection up to IP68. AxiForce fans also have small form factors that support variable installation, which enables greater application flexibility, a high cooling capacity, and the ability to network with device logic. As such, they are especially well suited for use in industrial control cabinets.
Can you tell us a little about your highly efficient GreenTech Electronically Commutated (EC) technology?
GreenTech is a philosophy that reflects our simple but clear approach that each new product must surpass its predecessor both economically and ecologically. With over 20,000 different products this is not always an easy task, but our engineers set new standards year after year with increasingly powerful and efficient motors and fans that consistently raise the bar.
Almost all of our products are available with GreenTech EC technology which provides customers with benefits including higher energy efficiency, lower maintenance costs, a longer service life, and sound reduction. A growing number are also available with GreenIntelligence IoT networking and digitalization capabilities. GreenTech EC technology represents a combination of commutation strategy and motor design. It features a unique construction that completely integrates the electronics into the motor to deliver the same footprint as many of our AC equivalent fans and low-noise operation with minimal structure-borne noise. GreenTech EC fans can be used absolutely anywhere and are suitable for operation in both single- and three-phase AC and DC systems.
What do you think is next in terms of compact fan design and performance trends?
I see a continuing effort to achieve top performance, high efficiency, low noise (this is a big one), low vibration, and economically competitive fan and blower solutions. As semiconductor technologies continue to evolve, electronics packaging power densities and data center concentrations will continue to increase, which will create increasing heat flux demands that fan and blower OEMs will have to innovate to keep up with.
Think about how CPUs in computers have changed. Twenty years ago, they might have dissipated 20–30W of power, but now, computers that are the same size or smaller employ CPUs and GPUs up to 200–300W. Designers keep trying to make computers as fast and as powerful as possible in as small a package as possible. This significantly increases the thermal challenges because it increases the impedance of a system and directly affects fan or blower selection.
ebm-papst & RS: Trusted Partners for Compact, Quiet, and Efficient Electronics Cooling
ebm-papst has more than 60 years of experience designing and developing ventilation and drive technologies engineered to provide efficient, economical solutions for commercial and industrial electronics applications. They are widely renowned for strengths including high quality, efficiency, reliability, and performance as well as innovative R&D, sustainability, and customer support.
RS works closely with the ebm-papst team, offers an extensive range of the company’s thermal management solutions — including compact axial fans, diagonal fans, centrifugal fans, and AxiForce fans — and can help you identify the optimal cooling solutions for applications including factory automation equipment, control cabinets, lighting, HVAC systems, and digital signage.
For more information about ebm-papst, please visit the ebm-papst storefront on the RS website. For assistance selecting and deploying ebm-papst compact fans in your application, please contact your local RS representative at 1.866.433.5722 or reach out to the RS technical support team.