A conversation with Jean-Marc Hubsch, Engineering Manager, ATEX and Functional Safety Manager, Encoders and Position Sensors, Sensata Technologies.
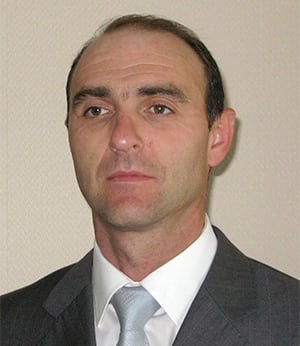
Jean-Marc Hubsch
Engineering Manager
Sensata Technologies
Engineers designing systems for industrial and factory applications are adopting functional safety design practices to reduce the risk of system failures. Such failures can result in damage to personnel and equipment which can be costly to an organization, monetarily and otherwise.
Globally, personnel safety is a paramount priority, and a prerequisite for any industrial application. International safety standards help unify a global network of industrial operations. However, manufacturers and systems designers have been slow to adopt all standards as the complexities of their requirements can be difficult to comprehend and incorporate, while maintaining profitability.
One of RS’s supplier partners, Sensata Technologies is a leading global supplier of sensing, electrical protection, control and power management solutions with operations and business centers in 13 countries. Sensata’s products improve safety, efficiency and comfort for their customers and end-users who benefit from the incorporation of their safety encoders in industrial automation applications.
Jean-Marc Hubsch is the engineering manager for encoders and position sensors for Sensata Technologies and is based in Strasbourg, France.
Can you provide an overview of functional safety encoders? What are they used for and what function do they perform regarding machine automation?
The primary role of encoders is to ensure safe speed monitoring. Encoders ensure that machinery movement is well controlled when the operator or other personnel come in proximity of the machine to perform any intervention.
For example, in a bottle-filling operation, encoders can help an operator interact with a machine to correct or make adjustments. The encoders automatically adjust machine movements to protect against any harm to personnel as they attend to the machine or equipment.
Encoders are built on a pure hardware architecture that make the devices robust, providing real-time information against a safety fieldbus interface (industrial computer networks used for real-time distributed control).
Encoders must be designed to accommodate and avoid any delays in transmitting information. Such delays can greatly impact productivity and be detrimental to throughput efficiency. Digital outputs help customers keep a high-immunity signal transmission and use the digital interface to simplify safety applications. A safety encoder also avoids sensor redundancy, reduces integration size, mechanical complexity, and may be configured and integrated with simplified wiring.
Sensata safety encoders help achieve safety objectives with confidence. Sensata globally has the broadest offerings for safety incremental encoders considering all the mechanical configurations multiplied by the unique digital (HTL or TTL) electronics with SIL3/PLe, Cat.4. ratings. In an industry-first, our encoders feature digital and analog sine/cosine signal output options. The encoders provide information to achieve a safe speed, direction and position.
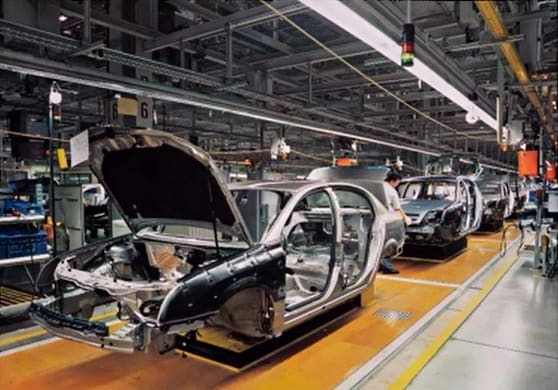
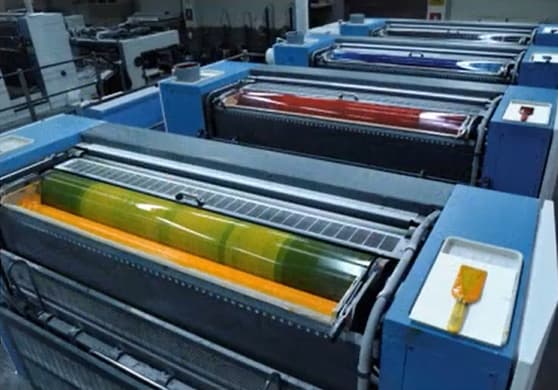
In the context of machines and industrial equipment, what risks do they help reduce or eliminate?
Machines must not pose unacceptable risk. However, in the real world, zero risk is not always possible. The use of industrial controls such as safety encoders and other sensors reduce danger in machines and enable an acceptable level of risk that would otherwise be difficult to achieve.
If safety is dependent on control systems that include encoders and sensors, such systems must be designed so the probability of functional faults is sufficiently low.
Best practices in functional safety must be driven by the need to conform to industry standards and to protect against accidents. Also, functional safety drives an effective and productive operation that reduces downtime and avoids costly repairs to equipment. Manufacturers that utilize control devices, such as safety encoders and sensors, as part of their functional safety into their processes and equipment, will have advantages. One major advantage is achieving an internationally recognized safety rating that enables their products to be sold worldwide.
Can you explain industrial safety applications coding? What is meant by SIL3/PLe, Cat.4.?
SIL3/PLe, Cat.4. is the highest safety rating for industrial devices. Starting at the highest rating with a digital encoder allows the machine builder to introduce multiple less-highly rated devices in a safety loop where the objective safety level is around SIL2/PLe level. It is important to remember that the safety level of the system is only as good as its least reliable element. Installing a SIL3 encoder in an application where components have lower safety ratings will not result in a SIL3 system.
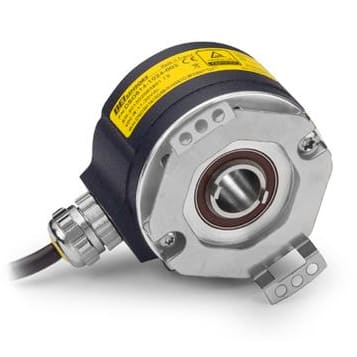
Functional safety encoders
What is the advantage in using functional safety encoders in a manufacturing environment or for OEMs to include such encoders on their equipment?
Safety encoders are mechanically compatible and wired in which makes their implementation very easy. The products are already certified. The process to get full machine certification is simplified for the customer.
For instance, the safety grade of Sensata encoders is certified by TÜV Rheinland, which allows customers to avoid doing the complex calculations themselves or being obligated to work with consultants in safety to independently certify the equipment. The result is superior safety at a reduced cost.
Is the objective of using functional safety encoders only to comply with industry standards and prevent accidents? Or does the function of these encoders go beyond that? Can you explain?
Meeting standards and preventing injury are very important parts of what encoders do, but their value extends to proven design and reliability. We have some high-value customers who need confidence and proven performance in improving their processes. They use our safety encoders to accurately detect material degradation and wear. Encoders can help to predict maintenance and signal impending failures before they occur which helps prevent unexpected downtime and improve profitability.
Overall, Sensata’s extensive experience in safety drives many projects on the way to autonomy in automated guided vehicle (AGV) deployment, and anywhere else where operators are forced to intervene in the machine’s operating area or must be present in the machine’s danger zone. The use of a safety encoder is a fundamental step to integrate more complex safety and integrated solutions. This is the real power of an engineering team.
Sensata Functional Safety Encoder Training 101
Reduce Risk with Sensata – BEI Sensors Functional Safety Encoders