Both new and established wind energy installations require specialized maintenance due to unique environmental hazards. As the industry continues to expand and evolve, operators and maintainers are increasingly looking to form trusted relationships with distribution partners that can make it easier for them to streamline their activities and become more profitable. Learn more about advanced and essential maintenance solutions for offshore wind turbines and how RS supports this sustainable energy market segment.
Veronica Maxted, Director of Renewables at RS Group
Wind turbines are an increasingly common sight in the hill, plains, and coastal regions of many countries. These elegant structures are visual manifestations of the burgeoning transition towards more sustainable energy sources and an essential tool in the global fight against climate change.
Offshore wind energy capacity in particular has risen steadily in recent years and currently stands at around 63,200 megawatts worldwide. In 2021 alone, more than 21,000 megawatts of offshore wind power were installed and connected to the grid, marking the beginning of a growing global trend towards bigger wind farms and more powerful turbines. For example, the Hornsea 2 offshore wind farm in the U.K., which became fully operational on August 31, 2022, features 165 turbines in an area spanning roughly 178 square miles and has the capacity to generate over 1.3GW, which is enough to power more than 1.4 million homes. This trend is evident in the U.S. as well. The U.S. Department of Energy’s 2023 Offshore Wind Market Report reveals that wind power remains one of the fastest-growing and lowest-cost sources of electricity in America, thanks in part to the Inflation Reduction Act, and that the potential generating capacity of the U.S. offshore wind energy project development and operational pipeline is now 52,687 megawatts, which is up 15% year-over-year. It also asserts that the U.S. invested $2.7 billion in the domestic offshore wind energy in 2022 and that 13 states now have policies that collectively support the generation of 112,286 megawatts of offshore wind power by 2050.
This trend is evident in the U.S. as well. The U.S. Department of Energy’s 2023 Offshore Wind Market Report reveals that wind power remains one of the fastest-growing and lowest-cost sources of electricity in America, thanks in part to the Inflation Reduction Act, and that the potential generating capacity of the U.S. offshore wind energy project development and operational pipeline is now 52,687 megawatts, which is up 15% year-over-year. It also asserts that the U.S. invested $2.7 billion in the domestic offshore wind energy in 2022 and that 13 states now have policies that collectively support the generation of 112,286 megawatts of offshore wind power by 2050.

Much of the public focus on the wind energy industry is centered on growth stats like the ones described above. Within the industry, however, there’s an equal focus on the routine maintenance and repairs that these installations require. In fact, due to current installation trends, wind tech or tower tech jobs are expected to grow by 96% by 2026.
Maintaining Offshore Wind Turbines
Offshore wind turbines present a special challenge since they’re typically located far from shore, which makes them hard to reach — and particularly so if weather and sea conditions aren’t ideal. In addition, they are constantly subjected to saltwater and corrosive marine atmospheres, and once maintenance crews are on-site, they must navigate the dangers of working at great heights in windy conditions.
To ensure the safety and efficiency of both their wind turbines and their maintenance personnel, operators rely on maintenance strategies and solutions ranging from advanced robotics, conditioning monitoring, and remote-control solutions to core maintenance solutions common to virtually all industrial applications, such as hand tools and hardware, personal protective equipment (PPE), multimeters, and lubricants, greases, and oils.
Advanced Maintenance Solutions
Advanced maintenance solutions include industrial condition monitoring and remote control equipment, including sensors, PLCs, remote I/O modules, industrial routers, industrial PCs, industrial Ethernet switches, and wireless access points. These types of solutions allow operators to remotely record, transmit, analyze, and leverage sensor data to identify — and potentially even rectify — electrical or mechanical issues before they damage equipment and cause unplanned downtime. As such, they also reduce on-site inspection requirements. In addition, condition monitoring solutions help maintenance technicians better prepare for on-site repairs, which can significantly improve on-the-job safety and efficiency and reduce the amount of time that maintenance personnel must spend in those hazardous environments. Product solutions available at RS and optimized for use in harsh industrial environments like wind farms include robust ifm Efector IP67 temperature sensors; inductive proximity sensors from Turck and Balluff, which respectively offer ruggedized form factors with a wide sensing range and quick-commissioning, non-contact functionality with an adjustable linearity range; secure, high-performance safety controllers from Schneider Electric; compact, powerful, and user-friendly safety PLCs from ABB; and intelligent, adaptable, and IP-rated PLCs from Phoenix Contact. Additional solutions include reliable remote I/O modules from Phoenix Contact and Moxa, plug-and-play FL Switch 1000 Series unmanaged Industrial Ethernet switches from Phoenix Contact, and Moxa’s secure EDR-10 industrial routers, rugged MC-1100 industrial PCs, and high-speed, industrial AWK-3131A Series wireless LAN access points (pictured left to right below).
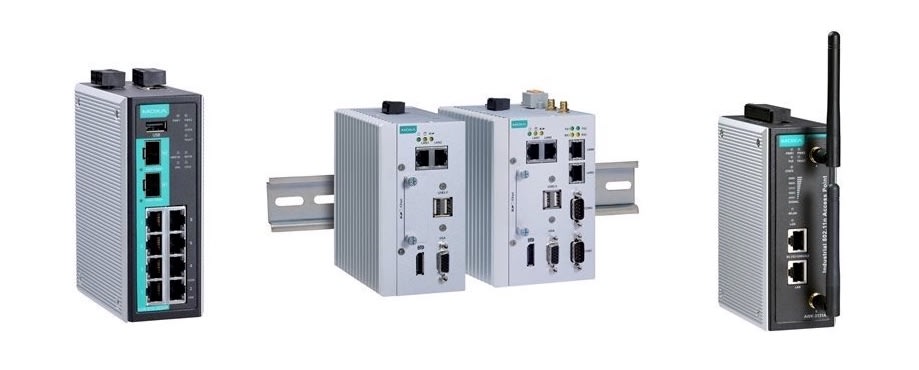
Essential On-Site Maintenance Solutions
Although advanced maintenance solutions like the ones described above help improve employee and equipment safety, uptime, and the cost effectiveness of wind turbine upkeep, maintenance teams are still required to board vessels and travel to offshore wind farms to perform various activities, such as gearbox and drivetrain repairs, electrical system tests, foundation and structural inspections, lubrication and fluid replacement, and general cleaning.
Since travel is required for on-site maintenance, offshore weather can be unpredictable, and downtime — even when it’s for essential maintenance — cuts into total revenue, the maintenance teams that service offshore wind turbines need to work quickly, efficiently, and safely while adhering to strict quality and compliance requirements. To accomplish this, they must be equipped with the right tools and equipment to perform the tasks at hand, including hand tools and hardware, facility cleaning and maintenance supplies, safety and personal protective equipment (PPE), multimeters, lubricants, greases, and oils, and replacement parts like AC drives, which — without predictive maintenance capabilities enabled by advanced condition monitoring solutions — cause an average of eight-plus days of downtime when they fail.
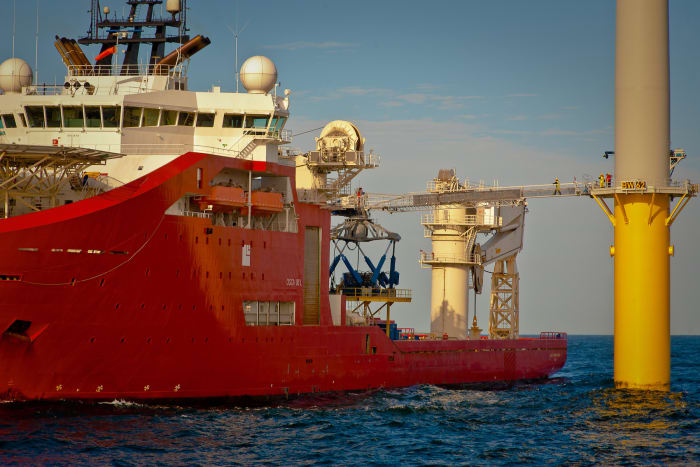
This is why operators and maintenance organizations in the offshore wind sector are increasingly looking to form trusted relationships with distribution partners that can offer carefully curated product ranges, speedy service, and new product innovations that make it easier for them to streamline their activities and become more profitable. The right partnerships can provide maintainers with quick, easy, and reliable access to essential on-site maintenance solutions and help protect them from supply chain shortages that could otherwise negatively impact maintenance operations, equipment safety, and profits.
RS has responded to the needs of the rapidly evolving offshore wind sector by offering an expanded range of essential maintenance solutions and services that make it easier for operators and maintainers to get the tools and equipment they need. As a global distributor with enormous buying power and operations in 31 countries around the world, RS can offer an extensive selection of relevant solutions at competitive prices and deliver them without delay.
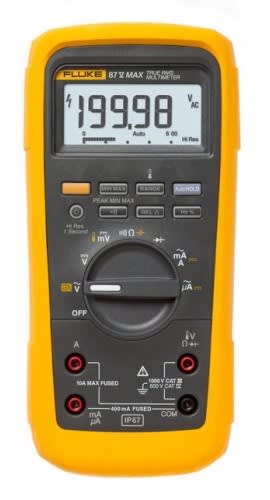
Product solutions available at RS and optimized for use in harsh industrial environments like wind farms include Fluke’s ruggedized and extremely accurate 87V MAX True-rms Digital Multimeters (pictured), which feature an IP67-rated, industrial-strength case with a removable holster that doubles as a test probe holder for easier one-handed operation, a backlit display for easy visibility in low-light environments, an extended battery life of up to 800 hours, and premium TL175 TwistGuard test leads with adjustable length test tips and WearGuard lead wire wear indicators for added safety. They also reliably withstand drops of up to four meters and temperatures extending from -40°C to +55°C.
Other essential on-site maintenance solutions ideal for wind turbines include lubrication solutions such as Klüber Lubrication’s Klübersynth’s GEM 4 N synthetic high-performance gear and multipurpose oil, which is engineered to satisfy the evolving requirements and increasing power density of modern gears, and its Klüberplex BEM 41-132 long-lasting, high-temperature grease, which is equipped with special additives that provide robust resistance to oxidation and protect against wear and corrosion.
RS: A Trusted Partner for the Rapidly Expanding Wind Energy Industry
The offshore wind sector is at an inflection point. It is growing rapidly in size and scale and adopting new maintenance solutions and strategies engineered to improve productivity, efficiency, and reliability and reduce costs. RS recognizes the need for strategic partners to help drive this momentum forward and is is responding to the rapidly expanding industry growth trends captured by universities like UC Berkely and the U.S. Department of Energy and further stoked by government initiatives like the Inflation Reduction Act, which modifies and extends the clean energy Investment Tax Credit, providing up to a 30% credit for qualifying investments in wind, solar, and energy storage.
Our commitment to fulfilling the needs of the wind energy industry is multifaceted, and we are actively investing in people, products, and processes to support future growth. To better serve the needs of the local wind energy industry, we have shifted our focus from simply distributing parts to providing total partnership for alternative energy companies. This shift helps wind and other clean energy customers improve the overall efficiency and reliability of their systems, ensure maximum operational safety and robustness, and embrace scalability while seamlessly integrating new technologies. It also helps provide customers with timelier and more streamlined access to the tools and equipment they need.
So, while we provide an extensive portfolio of proven products optimized for builders, operators, and maintainers in the wind energy industry, the value of which is further enhanced by our omnichannel ease of doing business, our support doesn’t stop there. We also provide a suite of service solutions that help these customers navigate the complexities of the industry, leverage opportunities, and overcome challenges throughout the design, build, and maintenance phases. We partner with forward-thinking industry organizations and participate in trade events, and we partner with education providers dedicated to cultivating skills and fostering innovation in millions of young people — many of whom will fill roles essential to the continued evolution of the sustainable energy industry, as well as the greater STEM industry, in the future.
For more information about the RS portfolio of maintenance solutions for alternative energy applications, including offshore wind farms, as well as expert insights into and advice about alternative energy and sustainability, please visit the embedded links throughout this article. For assistance identifying, procuring, and deploying maintenance solutions that can help improve the safety, productivity, and efficiency of your wind energy operations, please contact your local RS representative at 1.866.433.5722 or reach out to our technical product support team.
The offshore environment is brutal, as those at all familiar with offshore oil rigs can testify. Those hazards are fairly well understood and most of the requirements are known. Wind power systems all include rather large bearing systems for the prop and the rotation arrangement. And most of them also contain speed increasing gearboxes that must deal with the entire mechanical power. While gear maintaining is understood, it is neither simple nor easy. But given the huge effort needed for repairs or replacement of gearbox parts, preventing any problems is a huge priority, on the same level as the main bearing service. Generator and electrical generation systems have both mechanical and electrical requirements that are quite separate and require different skill sets. Likewise the physical controls systems.
The result is that, similar to many factories, different skill sets are required along with different tools.