In this installment of RS’s Ask the Expert Series, Siemens’ SITOP Power Supply Business Developer, Gregory Kateb, talks about power protection solutions for industrial automation applications.
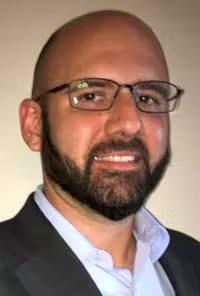
Hi Gregory. Please tell us a little bit about yourself.
Hi. I’m Gregory Kateb, the SITOP power supply business developer for Siemens. I have more than 17 years of experience in the critical power-protection industry and have held varying roles related to the commissioning, repair, and design of uninterruptible power supplies (UPSs). I’m especially well experienced in AC and DC UPS solutions for oil & gas, power generation, and heavy industrial equipment applications and have worked closely with OEMs, engineering, procurement, and construction (EPC) contractors, and end users in these industries.
Are there any machine, technology, or industry trends that are driving the development of new power protection equipment for automation applications?
The pandemic accelerated the employment of automated equipment processes and the digitalization of their monitoring and control processes. Digitizing the data generated by automation equipment and enabling remote connectivity and control allowed manufacturers to maintain productivity with fewer employees on-site, which has been a critical benefit for both staffing shortages and employee retention and safety.
All of the components that perform automated tasks, including PLCs, field devices, and operational technology network devices, require reliable power to operate. With less manpower immediately available to troubleshoot power quality issues on-site, it’s become almost a necessity to incorporate some form of power protection, such as redundant power, energy storage for back-up power, and/or the selective coordination of critical load fault protection. Smart power protection solutions with remote connectivity capabilities are also well suited for use in remote applications.
Are there a few key points of value that these types of power protection products offer?
Every minute of downtime in an automated process is profitability lost and, in some applications, it could be human safety issue as well. You can liken it to home security. If you and your family live in a secluded area like a farm or a mountain top, a door lock is more than enough protection for home security. But if you live in an urban area with a high crime rate, you would be taking a huge risk to not beef up your home security with one or more of the available options, which today range from solutions like the Ring doorbell to ADT monitoring and even a good old guard dog. There are obviously upfront costs to enhancing your home security, but the return on your investment — effectively protecting your home and your family — more than justifies those costs.
So, circling back to power protection for automation equipment. Say you have a remote pumping station for example. If you leave this automated process unprotected, it will actually cost you more in the long run because every power outage will require you to send a technician to the site to troubleshoot and repair it. And while they may be able to repair it immediately, costing you only a few hours or a day or downtime, there’s a real possibility that they could have to wait a day or two — if not longer given current supply chain constraints — to acquire the parts required for the repair, which could result in significant and costly unplanned downtime.
On the other hand, if you assumed the upfront costs of installing adequate power protection equipment, your pumping process would be able to soldier through short-lived power disturbances and outages and would also allow one of your operators to remotely connect to the power protection device to better understand if the issue was a one-off or a common occurrence. And if it were the latter, they could identify the issue, acquire the parts necessary to fix the problem, and schedule the downtime required for repair when it’s sure to be least impactful for productivity and profitability. So, the ROI on installing power protection equipment for automated processes like this more than justifies the upfront costs.
Are there any key characteristics that customers seeking out power protection solutions for automation applications should ensure their selections deliver?
Since the goal of power protection solutions is to protect critical automated processes and their operators from productivity losses and potential safety hazards, it’s vital to make sure that the solutions you’re considering are suitable for your application environment. Industrial environments are rife with both visible and invisible hazards, so you must consider your operating conditions during the engineering and product selection processes. It’s also important to carefully review product datasheets to ensure that your application’s operating temperature, humidity levels, and exposure to hazards ranging from weather to dust and dirt, oils and lubricants, and harsh chemicals won’t negatively impact the performance of your power protection equipment.
Are there two or more primary competing solutions in this market that you could compare and contrast?
Absolutely, AC UPSs and advanced industrial power supplies. If AC power is lost or distorted for even a few seconds, it can be enough to shut down automated industrial processes. To solve this issue, most operators use a UPS equipped with an energy storage device, typically a battery, to ensure that connected equipment can safely power down when affected by AC power issues.
The debate often is often whether to protect the AC supply using an AC UPS before the power supply, or to use a DC UPS after the power supply. AC UPSs are more complex and have more internal components that generate heat than a DC UPS and, as such, have a higher probability of failure. However, the vast majority of operators are more familiar with AC UPSs because AC power was predominantly used to power automation devices in the past. Nowadays, many of these same devices and the equipment used to digitize their data are powered by 24V DC power, which is much safer.
Our SITOP industrial-grade DC power products are best-in-class solutions for reliably supplying 24VDC. The heart of these products is a power supply that efficiently converts the incoming utility AC voltage to 24VDC. We can then equip them with one of our versatile and modular DC UPS offerings to provide ride-through protection specific to your application requirements. In addition, since modern energy storage technologies like lithium ion batteries and supercapacitors are available in the DC UPS portfolio, these devices can support longer operation than AC UPSs equipped with traditional lead batteries, and they require less to no maintenance to boot. They’re also easy to integrate into existing systems that already have a 24VDC power supply since they just add on to it and, unlike AC UPSs, which would have to connected upstream of the power supply, don’t require additional circuit protection like a circuit breaker. Another unique advantage is that SITOP devices support complete integration into our Totally Integrated Automation (TIA) open system architecture via PROFINET and our TIA Portal application, which enables the easy, seamless, efficient, and reliable interaction of connected automation components and offers unique opportunities for both engineering and troubleshooting.
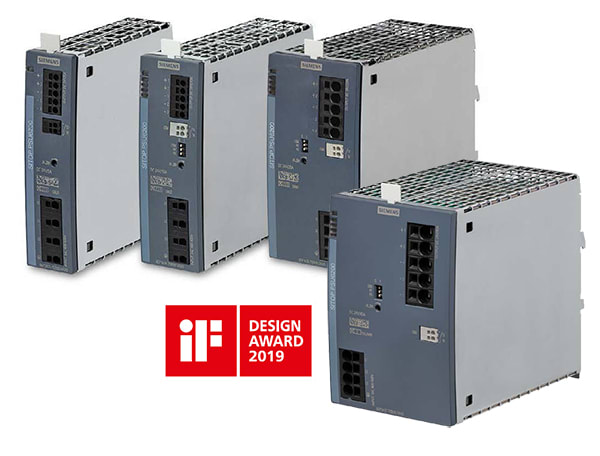
Is Siemens addressing power protection for automation applications any differently than its competitors?
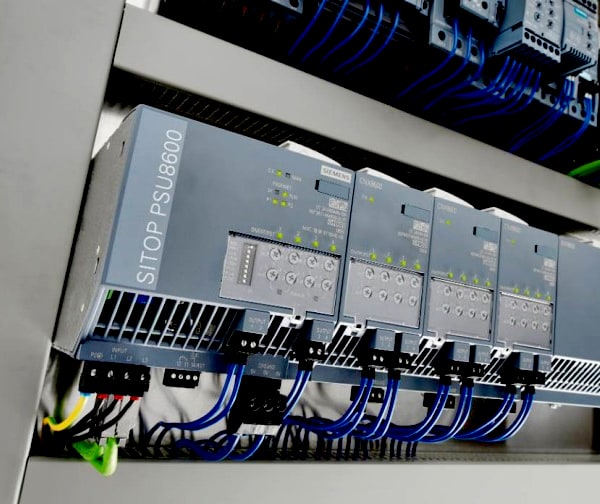
Our SITOP portfolio has unique products that were designed with digitalization in mind. For example, the SITOP PSU6200, UPS1600, and PSU8600 lines feature advanced diagnostic communication capabilities, accessible via an Industrial Ethernet or hard-wired connection, that competitors either lack or lag behind in. Giving operators the ability to log into their power protection devices securely, remotely, and reliably and gain a clear understanding of the connected equipment’s health effectively prevents potential downtime and profitability losses, which is already huge. But the SITOP portfolio also gives them the opportunity to go one step further, enabling them to share the same health status and diagnostic information they can access remotely with the automation system and, in doing so, enable automate controlled shutdowns of critical processes when power is unavailable, whether personnel is on-site or not.
Do you have any examples of these power protection solutions in action?
Yes, many, but I’ll just share one. El Paso Water is a utility company that was struggling to minimize downtime in their automated pumping processes using a 120VAC UPS. They were using multiple brands of 120VAC UPS systems, but all of them were bulky and didn’t provide any diagnostic information about the condition of the batteries tasked with safely powering down connected equipment including instrumentation, valves, and pumps. The high heat and dusty conditions at one of their pumping stations in the Chihuahuan Desert often caused the batteries to fail without warning, and since the systems weren’t intelligent, the pumping station could be down for hours before anyone knew there was a problem if operators were off-site. There was also no way to tell which personnel were needed to fix the problem until someone could go on-site to diagnose the problem, which led to lots of wasted man-hours for standby crews. Even worse, when the pumping station had no power and no backup power, the water supply to about 800,000 customers could be disrupted for hours and reserve tanks could empty or overflow.
We did a six-month trial of our SITOP UPS1600 system with backup battery power supplied by our SITOP UPS1100 and remote diagnostics that alerted El Paso Water to pending battery failures. Throughout the trial, the battery backup system tolerated the heat well without degradation and provided enough power to properly shut down the operation and alert central operations to the issue. This reliable backup power allowed the system’s PLC to remain energized for long enough to provide central operations with detailed diagnostic data that identified the exact cause of the problem and enabled them to send the right crew to the site with a solution ready, effectively minimizing downtime
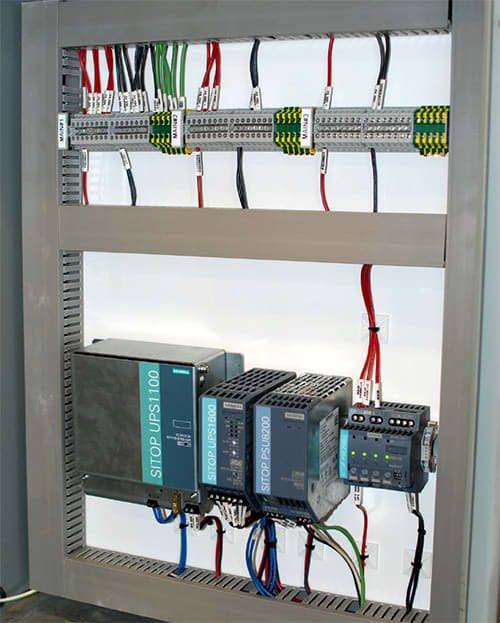
Two years after the installation, the batteries still hadn’t failed and there were no field calls to repair or replace the UPS. El Paso Water could remotely identify any issue that arose and quickly and efficiently deploy the right field technicians for the job. In fact, they were so satisfied that they even installed the SITOP UPS1600 at about 20 of their other pumping stations. And this is only one of hundreds of similar examples.
Protect your production power with Siemens and RS
Siemens is a leading global supplier of industrial automation technologies — many of which, including power supplies, DC/DC converters, UPSs, and add-on modules are in stock at RS. RS also has a team of highly trained representatives who can help you select the best power protection solutions for your industrial automation applications and walk you through the installation process to ensure that they will work when you need them most.
For assistance identifying and deploying Siemens power protection solutions sure to safeguard your automated industrial processes and reduce costly downtimes and repairs, please contact your local RS representative at 1.866.433.5722 or reach out to our technical support team.