Implementing smart machine safety systems has never been easier. Christian Olivares, Product Line Director – Safety at Banner Engineering, shares five simple steps for implementing and effectively capitalizing on the array of smart devices and intelligent networking platforms enabling manufacturers to better protect their employees and equipment, improve their productivity and efficiency, and reduce costly downtime and repairs.
Christian Olivares, Product Line Director – Safety, Banner Engineering
The future of manufacturing is smart, and one of the biggest benefits of smart manufacturing technologies is safety. Today, many equipment providers offer smart machine safety systems that can collect, transmit, and analyze data and provide operators, managers, and executives with valuable insights they can use to make important decisions about production, agility, efficiencies, health and safety, disruption resilience, and more.
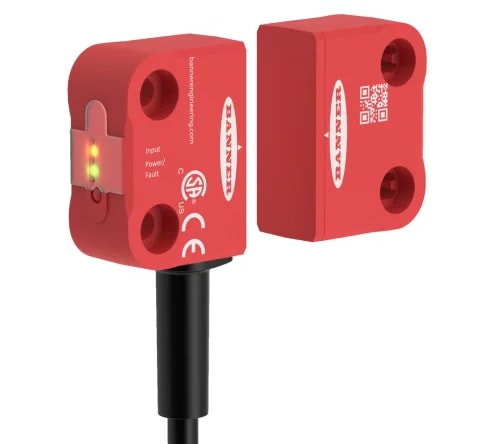
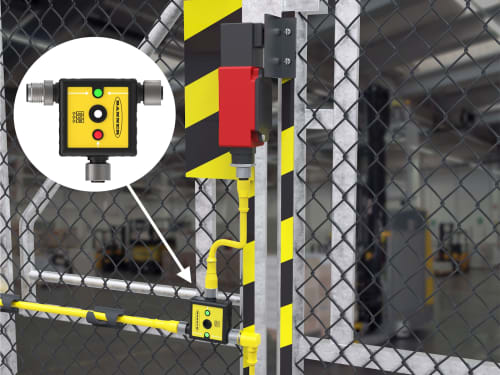
These systems enable manufacturers across the industrial landscape to minimize losses, increase profits, and unlock market opportunities that weren’t within reach just a few years ago.
But creating a smart digital ecosystem for machine safety can be somewhat of a challenge without the right foresight and guidance. So, here are five simple steps that manufacturers of all shapes and sizes can take to create a smart machine safety system capable of bringing their processes into the 21st century — along with all of the benefits and opportunities that entails.
1. Work From the Device Level Up
An effective machine safety system is not a singular entity; it’s an interconnected network of small, often overlooked devices that play a single role in a much larger system. Some of these devices already have smart technologies capable of collecting and transmitting in-depth diagnostic data designed into them, but many — like most door switches and emergency stop or e-stop switches — don’t. Most door switches, for example, only tell users whether the door is open or shut.
To make the most of a smart machine safety system, manufacturers must develop a detailed map of every critical data point in the system — including switches, light curtains, laser scanners, safety controllers, and relays — and note whether each device is capable of collecting and transmitting equipment data. If it’s not, they can either replace the device with a smart one or install an adapter capable of adding the device to their smart safety system.
Banner, for example, offers an adapter that can easily and economically integrate any device into our In-Series Diagnostics (ISD) intelligent networking system. With this valuable tool, legacy safety devices like door switches and E-stops can be integrated into a smart series chain for ease of wiring. Banner’s adapter can also identify the location of legacy safety devices, which leads to reduced downtime. However, it’s important to note that Banner’s ISD Connect adapter is only compatible with our machine safety systems, like our SC10 Series compact safety controller/relay hybrid for smaller machines or our XS26 Series expandable safety controllers, which have the capacity to adapt to a variety of machines, including large-scale machines with multiple processes. So, when you’re mapping your smart safety system, make sure that all your devices are compatible with whichever diagnostics platform you choose to adopt.
2. Simplify Cable Runs With Daisy Chains
Once all the devices in your machine safety system are integrated into the same intelligent networking platform, it’s time to review exactly how these devices are connected. Adding more elements to an electronic system typically requires additional cabling, which increases installation time, cost, and materials and, over time, can create connection complexities that put the integrity of the system at risk.
Another key benefit of implementing smart machine safety systems in automated production environments is the potential for network simplification. This is done through a technique known as daisy chaining, where cables are combined so that multiple devices share a connection line to the system controller.
Daisy chaining is hardly a new concept, and it is one that comes with inherent drawbacks — namely the ability to immediately diagnose system issues when a single device is stopping a machine. But in smart machine safety systems like Banner’s ISD system, each device has its own unique ID, which eliminates the main problem with traditional daisy chain systems.
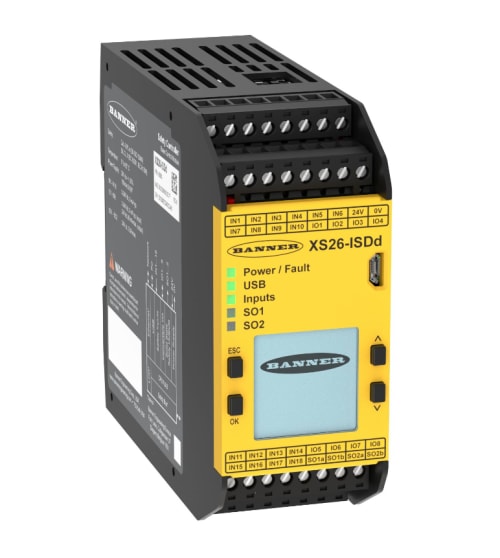
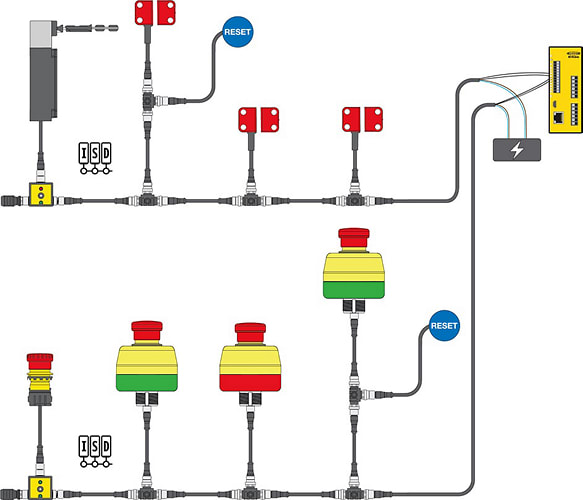
3. Consolidate Controller I/O Points
I/O consolidation goes hand in hand with cabling considerations in that the shared goal of each is to simplify network systems without sacrificing diagnostic specificity. In a traditional machine safety system, each device has a separate I/O point on the safety controller and/or PLC so users can quickly see where system disruptions are occurring. As these systems expand, operators can run out of I/O points, and at that point, manufacturers would have to invest in additional expansion modules, which could be costly.
Machine safety systems built on intelligent network platforms don’t have to worry about this issue. One single ISD chain, for example, which consists of only two wires connected to the safety controller, can monitor up to 32 devices. This significantly reduces the amount of hardware that goes into the control cabinet and greatly reduces the number of unique parts required for your safety system, which simplifies inventory and reduces both initial investment and down-the-road maintenance costs.
4. Adopt the Right Programming Tools
All the data in the world is of little use without capable programming tools that communicate the data in a clear, logical way that provides valuable insights. The market currently has no shortage of options available for manufacturers, and each comes with its own unique features that may or may not apply to the user in question.
To narrow down your search, it helps if you have a clear understanding of precisely what you want these tools to accomplish. A few features especially worthy of consideration include:
- Cost. Is the tool free, or does it require software licensing fees?
- Flexibility. Does the tool allow for easy expansion when adding new devices, and can it support devices from multiple manufacturing sources if applicable?
- Ease of Use. How quick and easy is it to integrate all of your devices into your intelligent networking platform?
Banner’s free safety controller software, for example, has an intuitive, icon-based, drag-and-drop interface that makes it quick and easy to set up, commission, reconfigure, and manage safety systems.
In addition, our XS26 Series expandable safety controllers include a new feature called AutoDetect ISD, which reduces system setup to just a few mouse clicks. When powered up, they identify all connected ISD devices as a baseline and report any changes to the PLC. AutoDetect ISD also supports dynamic safety applications, such as AGVs with removable carts or trailers and temporary subassembly stations on production lines.
Banner also offers SC-XM3 external memory drives that allow users to create a copy of their final machine safety program file and load it onto as many controllers as needed, which is especially beneficial for OEMs that build large runs of similar equipment.
If you find yourself questioning whether a particular programming tool is right for your safety system, contact the tool provider or one of their authorized distributors, like RS.
5. Establish Data Analysis Roles for Operators, Staff, and Supervisors
Just as important as the data collection system itself is establishing who will have access to the data. Since intelligent networking platforms allow users to easily share information with multiple systems, displays, and users, being acutely aware of where the data can be accessed and who is capable of viewing it is of the utmost importance.
These considerations also offer positive benefits for each actionable party. When analysis roles are clearly defined, each respective user will know exactly how to leverage the data presented to them in meaningful ways. For example, machine operators can use data to troubleshoot disruptions when they occur, while maintenance teams can use it to identify which machine parts to inspect, and supervisors can add diagnostic information to online dashboards to create future action plans. Collecting and analyzing machine data is an investment, and in order to effectively capitalize on that investment, all applicable parties must understand how the data impacts the bottom line as well as how it can help them with their roles or, in other words, what’s in it for them. The quicker everyone sees how much smarter and faster they work with the help of data-driven insights, the more quickly you can realize tangible results.

Improve Your Machine Safety System With Banner Engineering and RS
Banner Engineering offers more than 10,000 innovative solutions engineered to protect personnel, safeguard equipment, boost productivity, improve efficiency, and reduce costs — most of which are available through RS. RS offers an extensive selection of Banner Engineering products, including sensors, switches, lighting and indication, industrial data communications devices, and wire and cable, as well as a team of highly trained representatives who can help you select and implement the best smart safety systems for your manufacturing environment.
For more information about Banner’s In Series Diagnostics technology for machine safety systems, including their SI-RF Series safety switches, ISD Connect adapters, SC10 Series compact safety controller/relay hybrid for smaller machines, and XS26 Series expandable safety controllers, check out their Smart Machine Safety Systems product page. For assistance identifying, deploying, and maintaining Banner machine safety solutions and intelligent networking systems sure to protect your employees and equipment, improve your productivity and efficiency, and reduce costly downtimes and repairs, please contact your local RS representative at 1.866.433.5722 or reach out to the RS technical support team.