Several pervasive electronic design trends have resulted in the proliferation of compact and densely packed electronics that don’t leave much room for airflow or cooling devices but have high thermal management demands. We spoke with Wolfgang Laufer, the R&D Director of Compact Air Technology at ebm-papst, to learn more about cooling challenges, strategies, and solutions for today’s advanced electronic technologies, including factory automation systems, 5G network infrastructure, robotics, and data centers.
Three trends — increased electronification, higher power densities, and space optimization — have had a persistent influence on virtually every segment of the electronics industry over the past 10+ years and have resulted in the proliferation of compact and densely packed electronic designs that don’t leave much room for airflow or cooling devices but have high thermal management demands. The telecommunications and industrial automation segments have been particularly susceptible to these trends and continue to see more and more electronics packed into ever smaller form factors, which significantly increases overheating risks and the need for effective cooling strategies.
The electrical power drawn by electronic components, devices, and systems is dissipated as heat. But sustained high temperatures can damage circuit components, degrade their performance and reliability, and potentially even cause physical deformities, like warping, melting, and cracking, which can lead to short circuits, arcing, fires, explosions, premature failures, and injuries. In addition, the damage caused by overheating is usually irreversible, requiring the installation of replacement parts that could be subject to long lead times, result in unexpected costs and extended downtimes, and diminish productivity and profitability. As such, effective thermal management strategies are a vital element of every electronic design.
Compact axial fans are one of the most popular device- and system-level cooling solutions in virtually every segment of the electronics industry because they are easy to integrate and deliver high airflow rates. However, due to the impact of the far-reaching electronification, power density, and space optimization trends — which all heighten the need for thermal management — it’s becoming increasingly impossible to install more powerful fans or increase the number of fans and still comply with noise and space constraints.
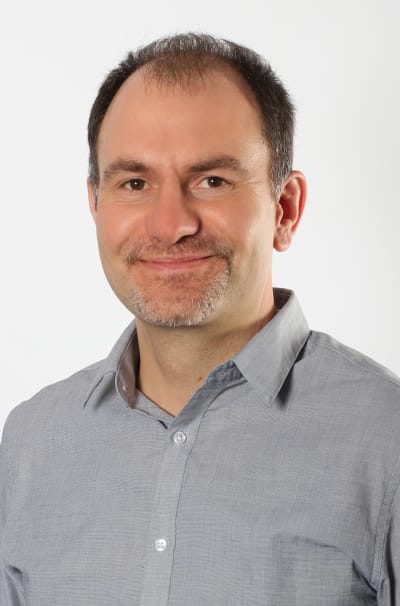
To learn more about cooling challenges, strategies, and solutions for today’s advanced electronic technologies, we spoke with Wolfgang Laufer, the R&D Director of Compact Air Technology at ebm-papst, a world-renowned manufacturer and supplier of innovative, sustainable, and intelligent air and heating technologies for commercial and industrial applications.
Hi Wolfgang. Please introduce yourself.
Hi. I’m Wolfgang Laufer, and I am currently the R&D Director for the overall development of compact fans in St. Georgen, Germany, which is located in the mountainous Black Forest region. I got my start in industrial mechanical equipment and precision engineering at the KERN-LIEBERS company, where I worked from 1994–1998, and then studied mechanical engineering and automation at the Furtwangen University of applied science. In 2001, I joined ebm-papst to complete my thesis work about liquid cooling concepts for high-performance chips and CPUs, and I have been with the company ever since. Over the course of my 23 years here, I have been employed in various fields, including finite element analysis (FEA), vibration optimization, and heat transfer. Later on, I implemented the first computational fluid dynamics (CFD) team for compact fan designs and became the R&D Manager for the aerodynamics and acoustics labs in St. Georgen. In 2017, I changed my role, moving from the predevelopment side to leading the product development team for compact fans, and I have been in my current position since 2020.
Q1. How have commercial and industrial electronic design engineers been overcoming the challenges posed by increased electronification, higher power densities, and smaller form factors for the last decade or so?
One common way to increase the cooling capacity of small form factor electronics equipped with extensive arrays of high-power-density components is to connect two compact axial fans in series. It’s possible for this configuration to feature two fans rotating in the same direction, but it is typically achieved using counter-rotating fans. This kind of two-stage fan design achieves higher pressure in principle, but the tandem rotors generate significantly higher noise levels, which means that fulfilling standards and guidelines for noise protection — including those issued by the Network Equipment Building System (NEBS), Occupational Safety and Health Administration (OSHA), and American National Standards Institute (ANSI) or European Telecommunications Standards Institute (ETSI) — is more challenging. In addition, passive noise reduction techniques, such as sound dampeners, are typically not an option, as they require too much space and drive up the design cost.
Q2. Why are telecommunications and industrial automation applications particularly susceptible to these challenges?
Given the pervasiveness of voice, text, data, image, and video transmissions, AI and machine learning trends, and the evolution of the IoT, 5G networks, and Industry 4.0 technologies, including robotics, the telecommunications and industrial automation segments of the electronics industry are experiencing a sustained surge in interconnectivity. As such, these systems are chock full of compact electronics equipped with extensive arrays of high-power-density components, which makes effective thermal management tricky. In addition, most of them are comprised of expensive assets expected to deliver long lifespans, and all of them have high uptime requirements, be it for safety, convenience, productivity, or profitability, which makes effective thermal management essential.
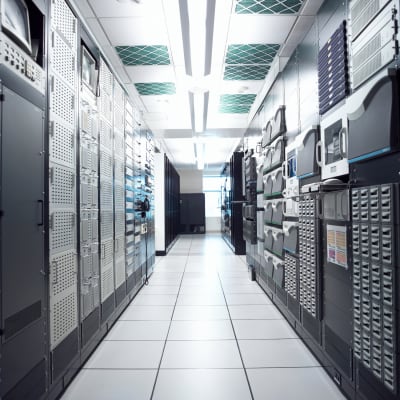
Q3. In response to these challenges, ebm-papst recently developed the new DiaForce fans, which feature a completely new-to-market design. Please tell us what’s unique about it.
Our new DiaForce 120mm diagonal compact fans feature an innovative design that combines the high flow rates of an axial fan with the high static pressure capabilities of a centrifugal fan. This inventive combination delivers the high performance of counter-rotating axial fans with less noise and significant power efficiency improvements to satisfy the challenging cooling demands of evolving digital connectivity applications.
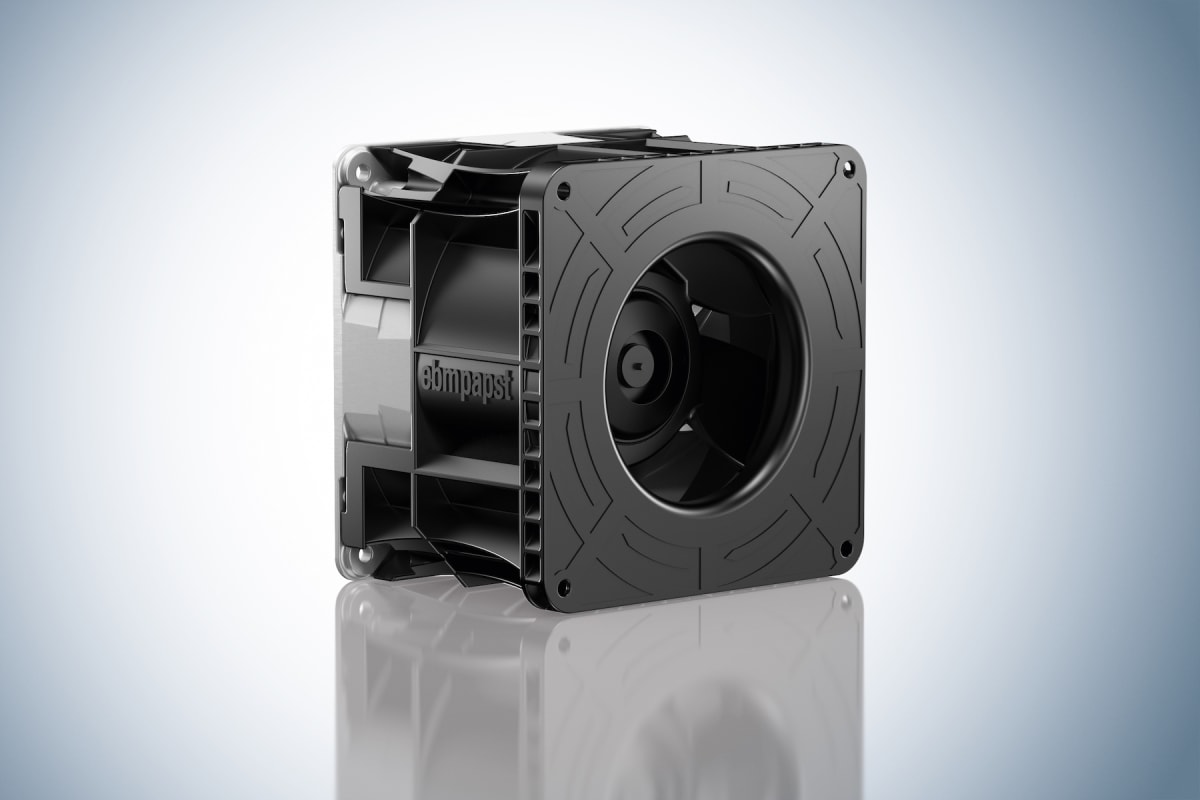
Developed to meet the ambitious specifications of a well-known electronics giant looking to cool its next-generation AI servers — but designed to overcome current and future electronics cooling challenges extending throughout the electronics industry — ebm-papst’s new DiaForce fans deliver up to 50% more air performance than the best single-stage compact axial fans currently on the market while generating 6–12dB(A) less noise. They also offer a significant reduction in power, much lower airborne tonal noise, less mechanical vibration, and a smaller and lower-profile footprint.
DiaForce diagonal compact fans feature an aerodynamically optimized design with unique impeller, housing, and inlet nozzle geometries; a larger outlet than intake opening with optimized guide vanes for higher pressure increase; a conical cover plate that rotates with the impeller; and a high-efficiency, state-of-the-art GreenTech DC motor. Air flows through the fans in both an axial and radial direction. Combining the key benefits of each design generates a higher static pressure than standard axial fans can provide while maintaining the ease-of-integration benefits of axial fans, with their axial-in/axial-out flow handling. The DiaForce blade tips pass directly into the cover plate which eliminates tip clearance and alleviates vortex generation in the clearance area (where there’s a considerable pressure gradient), resulting in significant noise reductions that deliver the quietest performance of any fan with this power density.
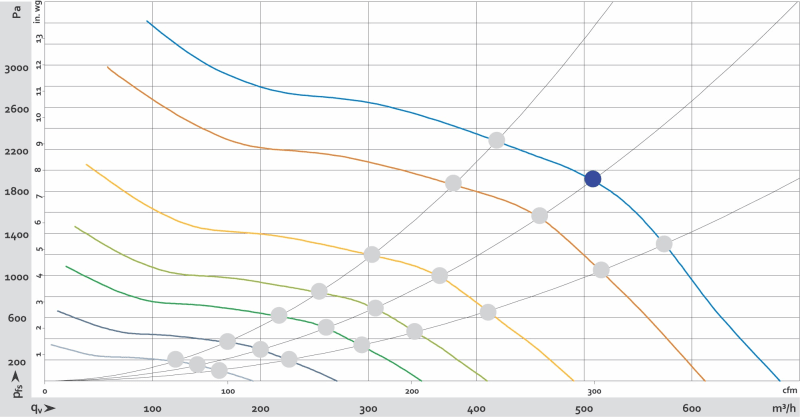
Q4. Very cool! (Pun definitely intended – chuckle or groan as you will.) Please tell us about the impact that these new fans will have on today’s advanced electronics applications.
Thanks to their unique design and the outstanding performance they enable, DiaForce fans can replace the larger, noisier, less efficient, and less integration-friendly counter-rotating fans commonly used to cool densely packed electronics in chassis. They can also create redundancies not possible with conventional single-stage fans that have to operate at their power limit to deliver adequate cooling and provide future-proof solutions for servers that manage massive amounts of data.
The higher air performance that DiaForce fans deliver is often not required in normal operation, as fans that cool electronics often operate at partial load. However, a sufficient power reserve is crucial to ensuring that the electronics continue to function sufficiently under conditions outside normal operation. For example, if the air conditioning in the room is faulty and the ambient temperature rises, there’s enough of a reserve available to speed up the fan as required.
As such, ideal applications include server, base station, mass storage, and cabinet cooling, as well as autonomous and AI technologies and 5G and IIoT networks.
Q5. Are there any other features of the new DiaForce fans that you’d like to share?
Additional features include a high-efficiency brushless DC (BLDC) motor, advanced integrated and optional functionalities, a convenient form factor, optional diagnostic tools, and compliance with all regulatory standards.
- DiaForce fans have a compact, three-core GreenTech DC motor engineered to drive substantial energy savings and high-quality, balanced impeller, and they are designed to deliver a long service life. They are also equipped with advanced internal cooling technology that dissipates heat from winding, electronics, and ball bearings to improve thermal management and are made without rare Earth elements for improved sustainability.
- Integrated functions include locked-rotor protection for improved safety, output signals proportional to motor speed, and speed control capabilities with multi-option control input. Optional functions include go/no-go and speed limit alarms, internal and external temperature sensors, analog control input, fast braking when power is cut, restart from back-spinning, and moisture protection.
- The series features a compact form factor with an industry-standard assembly geometry and supports quick and easy installation via four mounting holes on both the inlet and outlet sides.
- The optional FanCheck GreenIntelligence diagnostic tool enables maximum efficiency while also calculating the realistic service life of the fan based on its operating speed, temperature, and preset environmental parameters. These capabilities support predictive maintenance strategies, reduce equipment downtime and associated costs, extend equipment lifetimes, and deliver clear, competitive advantages for the interconnection and intelligent control of fans, drives, and systems.
- DiaForce fans are also compliant with all regulatory standards including NEBS, OSHA, ANSI, and ETSI.
Q6. Please tell us more about the fans’ state-of-the-art GreenTech DC motors.
The driving force behind DiaForce fans is a three-phase, energy-efficient brushless DC motor rated for up to 500W. The motor design is very compact and is equipped with a powerful microcontroller for intelligent motor control. It enables maximum possible torque in all load ranges and provides optimized efficiency and structure-borne noise. The integrated locked-rotor protection ensures safety. A configurable control input and various optional output signals are available as interfaces. Practical options include a signal go/no-go alarm, an alarm with a speed limit, and an internal or external temperature sensor.
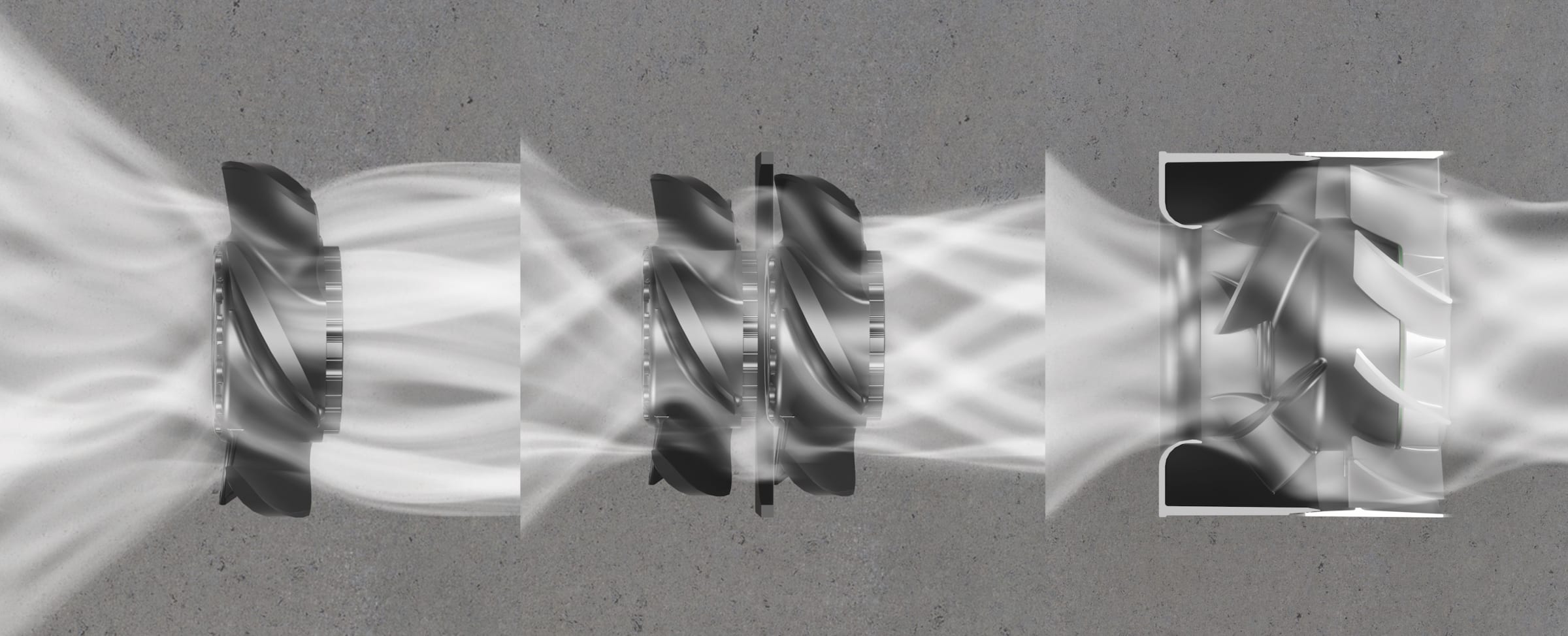
Q7. Please tell us more about ebm-papst’s proprietary FanCheck GreenIntelligence diagnostic tool.
When it comes to choosing the right drive or fan, it’s not just product characteristics, such as energy efficiency and performance values, that are crucial but also the intelligence and communication options that have been implemented. Examples of GreenIntelligence solutions for ventilation and drive technology include data acquisition using internal and external sensors, data processing, intelligent regulation of high-performance motor control systems and options for integrating the system into networks.
Thanks to condition monitoring, users can keep an eye on the operating parameters of their system at any time and carry out a better error analysis and optimization because the operating history is documented. Demand-oriented and predictive operation enables longer operating times, minimizing energy consumption and noise generation. Predictive maintenance allows needs-based service work to be planned so that longer service intervals and high availability can be achieved with a low number of downtimes.
The DiaForce fans’ optional FanCheck GreenIntelligence function enables users to implement intelligent maintenance concepts. In general, fans are designed so they don’t require maintenance during the life of the overall system they are cooling. However, fans are sometimes driven at unforeseen conditions, which can cause them to fail unexpectedly, and in those cases, they have to be replaced very quickly. Some service concepts also stipulate that all the fans in the system have to be replaced if one fan fails. This often leads to significant outlay due to the combination of material costs and labor costs, especially since service technicians have to travel to the installation sites. The FanCheck function from ebm-papst solves this problem.
FanCheck allows the replacement process to be planned cost-effectively and enables reduced replacement costs. It increases the availability of the devices and allows customers to specify how and when the fans should provide status information or warnings. It can also closely monitor the remaining service life or trigger a simple alarm when the remaining service life goes below a previously set value. And it’s easy to integrate into existing control systems, removing any potential hurdles to implementing intelligent and high-performance electronics cooling in information and communication technologies.
Q8. If I wanted to go ahead and implement DiaForce fans in my system, what would my options be in terms of models and physical and electrical performance characteristics?
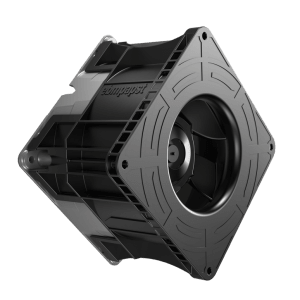
The new DiaForce diagonal compact fans from ebm-papst are currently available in a 120mm footprint that measures 119 x 119 x 86mm (L x W x H), moves airflow volumes of 680m3/h or 400cfm, consumes 395W of power, exhibits 48% overall efficiency, and has a nominal voltage of 48VDC with a range of 36–60VDC, a nominal speed of 17,200rpm, and operating temperatures extending from -20°C to +70°C (-4°F to +158°F). However, this is just the first of multiple DiaForce fan releases; 40mm, 60mm, and 80mm models are in active development and expected to be released to market later this year.
ebm-papst & RS: Trusted Partners in Innovative Cooling Solutions for Today’s Advanced Electronic Technologies
ebm-papst has more than 60 years of experience designing and developing ventilation and drive technologies engineered to provide efficient, economical solutions for commercial and industrial electronics applications and is widely renowned for strengths including high quality, efficiency, reliability, and performance, as well as innovative R&D, sustainability, and customer support.
RS works closely with the ebm-papst team, offers an extensive range of the company’s thermal management solutions — including the revolutionary new DiaForce fans — and can help you identify the optimal cooling solutions for applications extending from factory automation systems, 5G network infrastructure, robotics, and data centers to control cabinets, lighting, HVAC systems, and digital signage.
For more information about ebm-papst, please visit the ebm-papst storefront on the RS website. For assistance selecting and deploying the new DiaForce 120mm diagonal compact fans in your application, please contact your local RS representative at 1.866.433.5722 or reach out to the RS technical support team.