New regulations set to take hold in the coming years require food and beverage manufacturers to operate cleaner, safer, and smarter than ever. Spencer Webb, an application engineer at RS, dives into these challenges and introduces six solutions that, in addition to bringing you into compliance, will help you operate more effectively and efficiently than ever before.
Spencer Webb, Application Engineer, RS

The food and beverage industry, which encompasses the agriculture, food service, food distribution, and food marketing sectors, is one of the largest and most vital in the nation. In 2022, the U.S. food and beverage industry was worth about $1.4 trillion, a roughly 5.5% share of the national GDP, due in large part to contributions from the food and beverage manufacturing industry, which is consistently the second-largest contributor to the overall industry value behind food service.
The food and beverage manufacturing industry comprises many different markets. The meat processing and beverage manufacturing (including brewing) markets account for approximately 35% of the overall industry. The next largest are the dairy, baked goods, prepared food, and animal food markets. And while each of these markets has its own unique demands, each also features machine designers and builders, manufacturing facilities, engineering managers, and maintainers who must contend with similar overarching challenges — namely, stringent safety and compliance regulations.
From foodborne illnesses and food waste to the health and safety of facility workers, there are clear and countless risks involved in food and beverage manufacturing that necessitate extensive regulation, and the challenge of remaining compliant is only growing more acute.
The FDA recently made a series of updates to the Food Safety Modernization Act (FSMA) that focus on tracking and tracing and give manufacturers until January 2026 to comply. The new requirements create a standardized approach to additional traceability recordkeeping for people who manufacture, process, pack, or hold foods included on the food traceability list (FTL) and apply to both domestic and foreign firms that produce food for U.S. consumption or otherwise participate in the national food and beverage supply chain. These updates are also a crucial aspect of the FDA’s new Blueprint for the New Era of Smarter Food Safety, which lays out the agency’s plan to leverage smart technologies to further enhance traceability, improve predictive analytics, reduce food contamination, improve response times to outbreaks, address new business models, modernize retail operations, and foster the development of stronger food safety cultures. Together, these new regulations should accelerate the timeline for the identification and removal of potentially contaminated food from the market and reduce the number of foodborne illnesses and deaths, which are still prevalent despite a spate of existing regulations. According to the U.S. Centers for Disease Control and Prevention, approximately 48 million people get sick each year from foodborne diseases, around 128,000 of those are hospitalized, and roughly 3,000 die.
Maintaining compliance with these new regulations will require organizations throughout the supply chain to futurize their facilities and embrace digital transformation. And while that means that many manufacturers and other members of the food and beverage supply chain will need to make significant investments in technological upgrades, the smarter, more interconnected systems they create will make processes significantly more efficient and effective. This will have a tremendous impact on product quality, productivity, and profitability in addition to standards compliance — and not just with the new FDA tracking and tracing requirements.
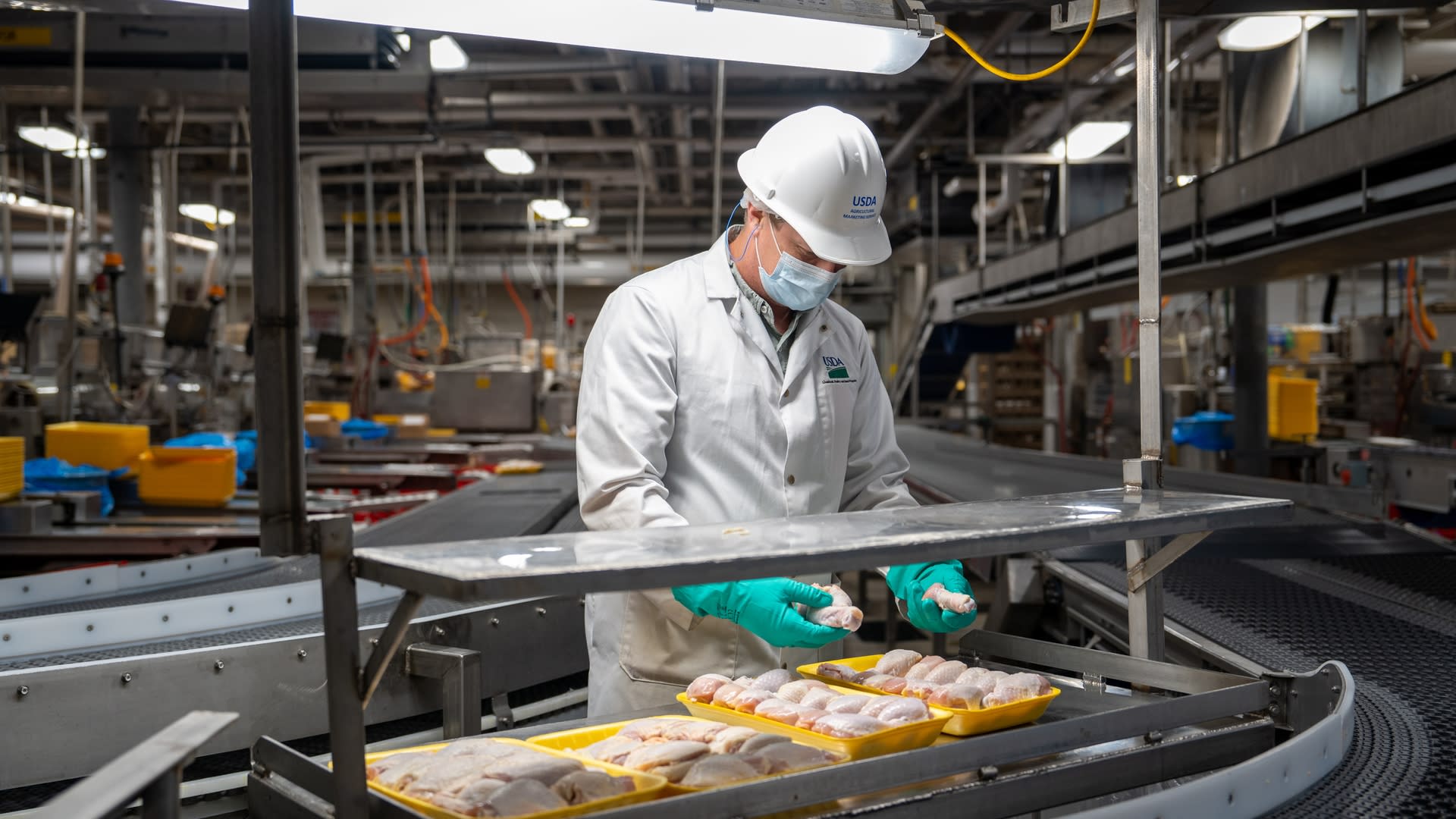
Organizations throughout the food and beverage supply chain must also comply with a number of other regulations pertaining to food safety, equipment and facility sanitation, quality control, labeling and packaging, environmental stewardship and sustainability, and employee and equipment safety. So, while connected technologies like RFID systems are essential for satisfying both these and the new tracking and tracing requirements, machine guarding and safety devices — including safety sensors, pneumatic and fluid controls, motors and motor controls, safety switches, and enclosures — are equally essential for mitigating various risks, preventing accidents, and ensuring compliance with industry standards. And like smart technologies, they also offer a number of additional advantages, including helping to maintain cleanliness, reduce workspace clutter, boost employee morale, and minimize operational downtime — all of which are especially beneficial in the food and beverage manufacturing and packaging industry since hygiene, efficiency, and cost-effectiveness are so crucial to success.
As such, the food and beverage industry is contributing to significant growth in the global food processing and handling equipment market and global machine safety market. The global food processing and handling equipment market was valued at $130.6 billion in 2021 and is expected to grow to be worth $175.1 billion by 2026, while the global machine safety market is projected to advance from an estimated valuation of $10.3 billion in 2022 to a valuation of $11.5 billion by 2031, due in large part to rising demand for packaged foods, worker safety, and strict regulatory standards.
Safety Sensors
Safety sensors are used to monitor the status of doors, hatches, windows, and other moving objects to ensure safe access and protect people and machinery in hazardous areas. They come in a wide variety of form factors and functionalities, but they’re all designed to control or prevent access at times of high risk and even stop machinery when necessary to keep personnel, equipment, and processes safe.
Safety sensors like safety ropes and gates are designed to prevent or monitor movement in hazardous areas. Safety switches are commonly used to supply or cut power to hazardous machinery depending on whether the coast is clear or if people or vehicles are passing through the area. Other safety sensors, including camera and radar systems, are used to monitor movement and anticipate risk. Smart safety sensors collect vital data so you can better understand your safety profile and identify where certain protocols are needed most. These devices are especially crucial in food and beverage manufacturing facilities, where there’s a lot of dangerous machinery, and limiting access to certain areas is crucial to maintaining safe, contamination-free packaging.
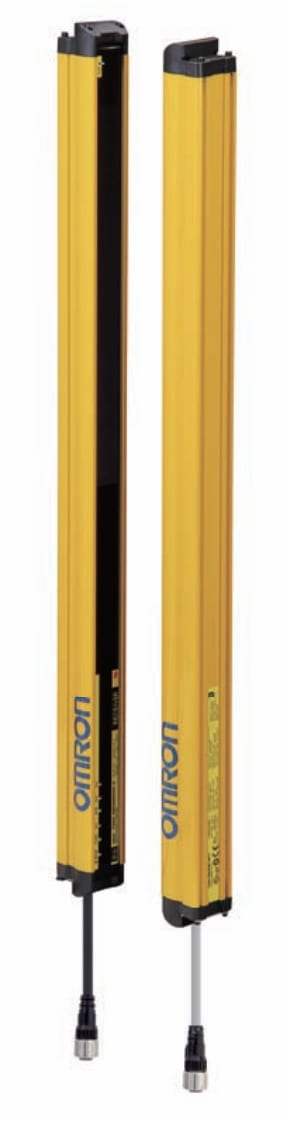
Light curtains are one of many crucial safety sensors in these types of environments. These photoelectric sensors consist of a transmitter and a receiver. The transmitter is equipped with LEDs that send infrared pulses released at a specific frequency to the receiver in sequence (e.g., from top to bottom). The receiver paired with the transmitter expects these pulses in the right sequence and timing, which all but eliminates the possibility of interference from other light sources. When an opaque object, like a person or vehicle, passes in between the transmitter and receiver, it interrupts the reception of the pulses and triggers the connected equipment to stop. And unlike other photoelectric sensors, light curtains have self-monitoring circuitry, which means that, in the event of a fault in their operation, they’ll emit an automatic stop signal that will prevent the connected equipment from functioning unless an effective safeguard is present. They are often deployed specifically around a particular piece of equipment or on the perimeter of a larger workspace and are used to stop machinery when a person is detected nearby.
Omron Automation F3SG-RE Series light curtains are simple, reliable, and cost-effective safety solutions ideally suited for food and beverage industry applications ranging from processing to packaging lines. They have slim housings that are easy to mount, operate, and maintain in a variety of application environments, and they only require four wires for the minimum configuration, which makes it quick and easy to build a safety circuit. They also feature smart-click cable connections that enable fast setup and ensure the correct torque for IP67 compliance and are rugged enough to deliver reliable performance in operating environments subject to hazards including dust, vibration, and washdowns. Their simple on/off detection reduces errors to improve productivity, and they offer QR code indication for easy online troubleshooting. They also offer options including 14mm finger protection and 30mm hand protection detection capabilities, safety field heights ranging from 160–1,950mm, 8–135 beams with a 10 or 20mm gap, a maximum safety range of 10 or 20m, and response times extending from 5ms to 15ms to keep personnel and machinery safe.
Pneumatics and Fluid Control
Pneumatic and fluid control solutions provide users with a safe, versatile, and cost-effective way to power a wide range of systems. Pneumatic systems use the flow and pressure of air or compressed gases to drive automated equipment. And because they’re powered by air or gas rather than oils or hazardous liquids, they can help food and beverage manufacturers work towards their sustainability goals and act as powerful yet cost-effective tools for achieving and maintaining FSMA compliance. The right solutions can help keep food and beverage equipment and products clean and safe from cross-contamination, they reduce the risk of tainted food and other incidents that could lead to costly recalls and harm consumers as well as manufacturers’ reputations.
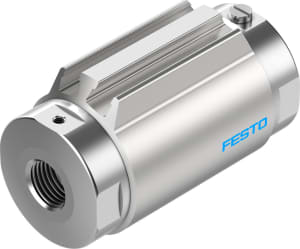
Festo VZQA pinch valves are ideal for food and beverage manufacturing and packaging applications and give you the ability to control the flow of materials including granulate, fluids containing solids, and highly viscous or abrasive products. These modular valves are compact, quick and easy to install, highly configurable, and easy to clean and are available with rugged, corrosion-resistant stainless steel or aluminum housings that deliver durable performance in challenging operating environments with temperatures spanning -5°C to 150°C. They’re also available in normally open and normally closed models with a variety of fitting connections, flow rates extending from 0.7m3/h to 18m3/h, three housing cover materials, three shut-off element materials, four nominal diameters spanning 6–50mm, and optional end-position sensing for broad application suitability.
Motors and Motor Control
Motors and motor controls are complementary products used throughout food and beverage manufacturing and packaging processes, including washdown areas, so they need to be watertight and washdown-ready for sanitary compliance. Industrial motors are used to convert electrical power into the mechanical power required to run applications including conveyors, pumps, and air-moving systems, while motor controls manage motors by controlling their direction (i.e., forward or reverse), regulating their speed and torque, and protecting them against electrical failures.
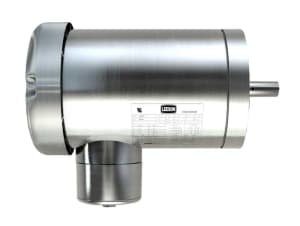
LEESON Motors designs and develops a wide range of washdown-ready motors, including the Extreme Duck Ultra washdown duty AC motor. These motors are purpose-built to help avoid downtime and reduce replacement costs in rugged industrial applications and feature an exterior made of 300-series stainless steel to resist corrosion and robustly withstand high-pressure washdowns and harsh chemicals. They also offer a patent-pending rotatable conduit box and are fully encapsulated inside and out to achieve a robust, IP69K watertight seal capable of keeping out all sorts of contaminants, including water, oil, and chemicals. Additional features include enhanced shaft seal technology that enables installation in any orientation, color-coded, non-wicking motor leads, LEESON’s patented IRIS inverter-rated insulation system, 10:1 constant torque operation, and BISSC, UL, CSA, and CE certifications.
RFID Wireless Data Communications
Radio frequency identification (RFID) technologies, including smart labels, QR codes, and barcode scanners, use radio waves and electromagnetic coupling to wirelessly transfer data about the identity and location of a variety of objects. They’re akin to barcodes but aren’t limited to line of sight and can be read up to 30m away. RFID technology supports full transparency, allowing manufacturers, regulatory bodies, and customers to track the journey of products throughout the supply chain, from farm to table, which is essential for compliance with the new FSMA tracking and tracing requirements.

The Balluff BIS M Series Industrial RFID System pictured here, for instance, supports global ISO standards, bus systems, and high data transmission speeds, is rated for washdown environments, and is available with high-temperature, metal-mount, hardened, and disposable tagging options and a variety of data carriers and read/write heads. It’s also quick and easy to install and compatible with IO-Link components. These features make it especially useful for close-range tracking and tracing applications extending throughout the global food and beverage industry, ranging from tracking food products through distribution and storage to monitoring the shelf life of food and ensuring that foods remain a safe temperature during transportation and storage. Balluff also offers industrial cable assemblies and mounting hardware necessary for installation.
Safety Switches
Safety switches are an essential machine safety solution that, per the National Electrical Code (NEC), must be installed in all commercial and industrial machinery applications. Safety switches are used to open and close circuits to ensure the safe operation of machinery and are available in a variety of different designs — including general and heavy duty, fusible and non-fusible, single- and double-pole single throw, and single- and double-pole double throw — to satisfy a broad range of application demands. They are often installed in a machine’s control circuit to stop or alter its operation when triggered and are also used to safely and reliably disconnect power from a machine so workers can safely perform maintenance.

PSENmag Series safety switches from Pilz are designed to keep personnel and equipment safe in a variety of challenging operating environments, including food and beverage manufacturing and packaging facilities. These switches are Ecolab certified, which means that they’ve undergone comprehensive, science-based quality and performance testing to ensure compliance with food safety protocols. Another reason PSENmag Series safety switches are ideal for food and beverage applications is that they’re available with IP65, IP67, and IP69K sealing for use in heavy-soil and washdown environments and are tested and proven to withstand abrasive cleaning solutions, including highly alkaline and acidic cleaning agents, such as P3-topax 19, P3-topax 56, and P3-topax-66, which are commonly used throughout the industry to maintain strict sanitation standards.
Pilz PSENmag Series magnetic non-contact safety switches are used to monitor the position of machine guards in accordance with EN 60947-5-3 and are commonly deployed in food and beverage packaging equipment. They have a compact design available in circular and square geometries to optimize installation space and offer connectors and cables designed to support all mounting styles and angles and enable flexible, fast, and convenient installation. They’re also durable and long-lasting, resistant to vibration and impact, and available with plastic or stainless steel housings, the latter of which is additionally resistant to harsh conditions including extreme temperatures.
Enclosures
Enclosures provide critical protection for the various industrial control system components essential to food and beverage manufacturing and packaging operations, including wires, cables, connectors, fans, and PLCs. Enclosures designed for food and beverage applications are often engineered to withstand high-pressure and high-temperature washdowns, resist bacteria growth and chemical absorption, and prevent
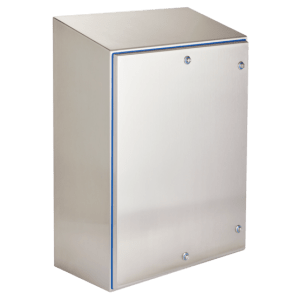
corrosion resulting from frequent cleaning and sanitizing.Many also have streamlined hygienic designs that prevent fluids from pooling on the enclosure and bacteria from harboring in nooks and crannies.
nVent HOFFMAN’s HyShed Series enclosures are made of stainless steel for durability and improved cleanability and feature crevice-free latch surfaces to reduce possible catch points that could harbor bacteria, a brushed #4 finish compatible with dairy industry applications, and a 15° sloped top to prevent fluids or particulates from pooling and maximize back panel space. They also have an easily replaceable FDA-grade silicone gasket that helps resist bacteria growth and chemical absorption and can be opened with standard tools.
Overcome Food and Beverage Safety & Compliance Challenges With RS
The food and beverage industry is a robust part of the national and global economy and, due to the significant risks it presents spanning production to consumption, is subject to a wide and regularly evolving variety of safety and compliance regulations that affect everything from manufacturing and packaging processes to product storage and transportation.
RS offers a vast selection of electrical and electronic products designed to support process innovation, equipment, personnel, and product safety, and sustainable growth and success in the food and beverage manufacturing and packaging industry. Our portfolio of more than 78,000 in-stock and ready-to-ship solutions ideally suited for this industry includes the safety sensor, pneumatics and fluid control, motors and motor control, RFID, safety switch, and enclosure products we addressed here in addition to a wide variety of RS PRO products meticulously designed to help you overcome common food and beverage safety and compliance challenges at a cost-efficient price point. These solutions include high-quality, industrial-grade, and competitively priced sensors and accessories, such as sensor mounting hardware, panel-mount sensor cables, pigtail sensor cables, probes, sensor testers, industrial cable assemblies, like double-ended cordsets, and barcode readers.
RS also provides end-to-end support for food and beverage industry customers. Our team can help guide you through the concept, design, sourcing, purchasing, building, and maintenance stages and help you overcome common challenges ranging from retrofitting legacy equipment and designing for scalability to future-proofing maintenance processes and complying with evolving safety regulations, including the FDA’s new FSMA tracking and tracing regulations.
To learn more about how we can help you modernize your equipment, improve your processes, and achieve FSMA compliance, follow the embedded links to relevant articles from our RS Expert Advice Series. For assistance identifying, procuring, deploying, and maintaining products that can help improve the safety and compliance of your food and beverage operations, please contact your local RS representative at 1.866.433.5722 or reach out to our technical product support team.