Variable frequency drives (VFDs) are widely recognized as essential tools for improving energy efficiency in demanding commercial and industrial motor applications, but they’re not all created equal. Abe Fares, the OEM Area Sales Manager for the Gulf region at Eaton, addresses the math behind motor efficiency, introduces the unique benefits of Eaton’s patented Active Energy Control algorithm, and shares both internal and third-party testing data to help you select VFDs proven to deliver the innovative solutions you need to remain compliant and competitive.
Abe Fares, OEM Area Sales Manager – Gulf Region, Eaton
For nearly half a century, variable frequency drives (VFDs) have been used to improve energy efficiency in demanding commercial and industrial motor applications. VFDs — which are also sometimes referred to as variable or adjustable speed drives, adjustable frequency drives, AC drives, and inverters and are often used to replace across-the-line starters and soft starters — are motor controllers that drive electric motors by varying the frequency and voltage they supply. The frequency supplied to electric motors directly affects their speed, which is measured in rotations per minute. The higher the frequency, the faster the motor spins. But not every application requires that motors run at top speed, so driving the motor at the optimal speed for the application at hand can save a significant amount of energy.
Due to their longevity, VFDs are available from a number of trusted suppliers, each of which has at least a slightly different approach to VFD design and energy optimization. As VFD technology has evolved, so has its ability to reduce energy consumption, improve reliability, and extend equipment lifetimes. In recent years, though, the combination of industry regulations and customer demand for energy savings has really amped up the need for design innovation.
To satisfy these market demands, Eaton — an intelligent power company dedicated to helping customers manage electrical, hydraulic, and mechanical power more safely, efficiently, reliably, and sustainably — developed VFDs with a patented Active Energy Control algorithm. This unique algorithm reduces the input power of induction motors used to drive variable torque loads, like pumps and fans, and delivers even greater power savings and stability than other static or dynamic V/Hz control methods. This active control feature dynamically adjusts the motor’s operating point based on its load conditions, creating greater stability and saving up to 10% more energy than other manufacturers’ VFDs.
Here, we’ll take a look at the math behind the motor efficiency and stability improvements, the unique benefits of the Active Energy Control algorithm, and testing conducted to prove its efficacy and point you in the direction of products and people that can help you incorporate these advantages into your commercial and industrial motor systems.
The Math Behind Motor Efficiency
Most VFDs designed for induction motors employ power electronics switching technologies to supply variable frequencies of AC power, control the motor speed, and improve energy efficiency. The typical output voltage waveform is based on pulse-width modulation (PWM), which means that the amplitude, duty cycle, and periodicity of the PWM waveform determines the effective voltage and frequency of the VFD output. Voltage output, frequency output, and motor load are the three key factors that determine the operating point for VFD-driven motors.
In industrial applications with constant load requirements, a constant volts per hertz (V/Hz) ratio provides constant torque for the load. The constant V/Hz ratio corresponds to a linear V/Hz curve that’s established by connecting two points, the rated frequency (frated) and the rated voltage (Vrated), with a straight line. When this curve is applied, the voltage for a specific command reference frequency (fref) is equal to that frequency times the rated voltage divided by the rated frequency (fref * Vrated / frated).
In applications that use induction motors to power pumps and fans — like in HVAC and hydraulics applications — variable torque is needed to drive the motor load. The amount of torque required is based on the shaft speed of the motor, which is determined by the frequency of the VFD output. As such, the torque required to power a pump or fan at a lower reference frequency is lower than that for a higher reference frequency.
The linear V/Hz curve in these types of applications typically provides a higher than needed voltage, and especially when the reference frequency is significantly lower than the rated motor frequency. A such, many VFDs will apply a squared V/Hz curve, which typically results in a lower voltage for a specific reference frequency than the voltage output based on the linear V/Hz curve.
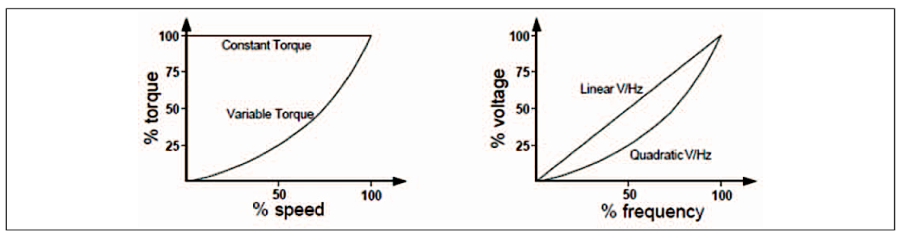
The primary benefit of reducing induction motors’ input voltage is that it also reduces motor core losses, like heat and noise, which are typically proportional to the square of the input voltage. Both linear and square/quadratic V/Hz curves are static V/Hz control methods, which means that the voltage output depends only on the reference frequency, not the motor load. So, if the motor load is low, the static voltage generated by either curve could be more than enough to power the load and, as such, generate core losses. But if the motor load is higher than what the static voltage can manage, the squared V/Hz control method can destabilize the motor and cause it to overheat or stall.
To address these concerns, Eaton developed a dynamic V/Hz control method — the Active Energy Control algorithm — which monitors real-time operating parameters, including the motor load and motor current, to optimize VFD output voltage for energy usage and motor stability.
The Benefits of Active Energy Control
Eaton’s Active Energy Control algorithm was developed to determine the optimal output voltage based on the reference frequency and the dynamic real-time parameters of the motor and ensure the stability of the motor.
The algorithm activates when VFDs are made to start a motor following a reference frequency or when a user enters a new reference frequency. It initially sets the drive output voltage at the same level as the voltage based on the linear V/Hz method for the same reference frequency to ensure the stability of the motor. The algorithm then incrementally reduces the voltage to optimize energy usage while simultaneously monitoring several real-time parameters to prevent motor instability. When the motor reaches its optimal operating zone, the drive output voltage stays at the same level until changes in performance parameters trigger new drive commands.
While it’s true that reducing the voltage output to a motor reduces its core losses, excessive voltage reductions can cause the motor current to rise, leading to instability and other losses, such as motor copper loss. VFDs equipped with the Active Energy Control algorithm continuously monitor the motor slip and motor current to prevent this from happening.
Changes in the motor load, and especially abrupt increases, can also lead to motor instability. Slower changes to the motor load cause the motor slip and motor current to change gradually. VFDs with Active Energy Control can detect both and adjust the voltage output accordingly to stabilize the motor and prevent losses, and much more quickly and effectively than many competing VFDs can.
Proven Energy Savings
Eaton compared the performance advantages of its Active Energy Control algorithm with other suppliers’ V/Hz control methods to demonstrate its superior stability and energy savings.
Stability Tests
Abrupt increases in reference frequency or motor load are the biggest challenges to maintaining stability because they require such a quick response. When we tested the Active Energy Control algorithm, it maintained stability under multiple operating conditions, through incremental frequency changes ranging from ±1Hz to ±15Hz, and through motor stalls, overcurrent trips, and overloads.
Energy Savings Tests
Eaton conducted energy savings tests in a lab environment with a 50hp motor driving a generator used to power resistor banks with values selected to mimic typical pump or fan loads. At 60Hz, the selected output power level of the motor was 37.5hp. At other reference frequencies, the output power was adjusted based on the frequency value and affinity laws. We used a three-phase power meter to measure the input power to the drive, compared it with the power value when using the linear V/Hz mode, and calculated a percentage value of power savings for each frequency tested, which you can see in the graph below. For comparison purposes, we also calculated the power savings percentages achieved by square V/Hz mode and flux optimization mode over the linear V/Hz modes.
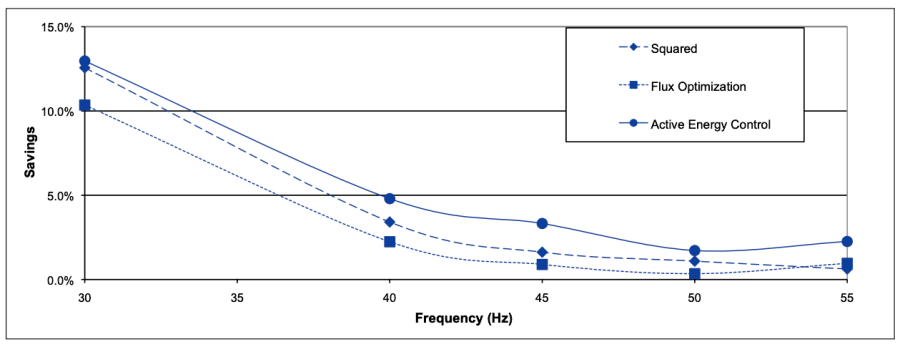
The test results demonstrated that the Active Energy Control algorithm enabled superior energy savings compared with existing static and dynamic V/Hz control algorithms, and the savings were more significant at lower reference frequencies.
We then tested our algorithm enhanced VFD in a real-world application, using a 50Hz model to drive a 50Hz motor that powered a centrifugal pump at a wastewater treatment plant. We recorded the VFD input power at 25Hz, 30Hz, 40Hz, 45Hz, and 50Hz in both linear V/Hz mode and the Active Energy Control mode and, as you can see in Figure 3, the real-life testing results matched our lab testing results and verified the superlative energy-saving capabilities of VFDs equipped with our Active Energy Control algorithm.
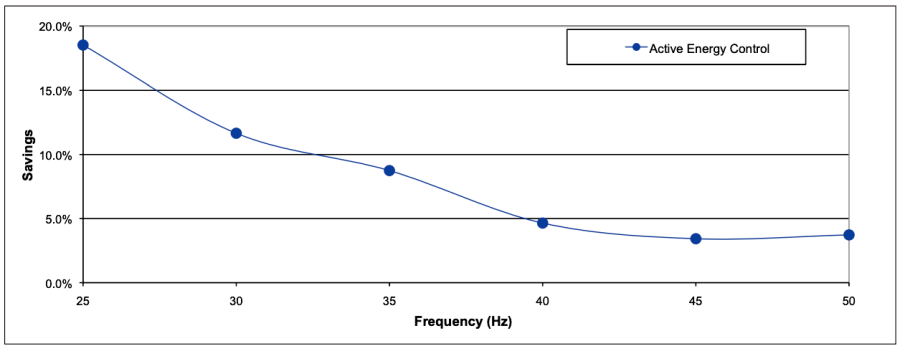
In addition, after conducting this internal testing, we had a third party compare our VFD’s performance to competing VFDs with energy control algorithms to verify our results. The third-party tester used the VFDs to power a 20hp motor used to drive a size 24½ blower and recorded input power values between 30Hz and 55Hz for various V/Hz control modes. Figure 4 shows the energy savings percentages compared with the input power of the linear V/Hz mode and also includes results for competing supplier’s VFDs with flux optimization mode and dynamic V/Hz control mode for comparison.
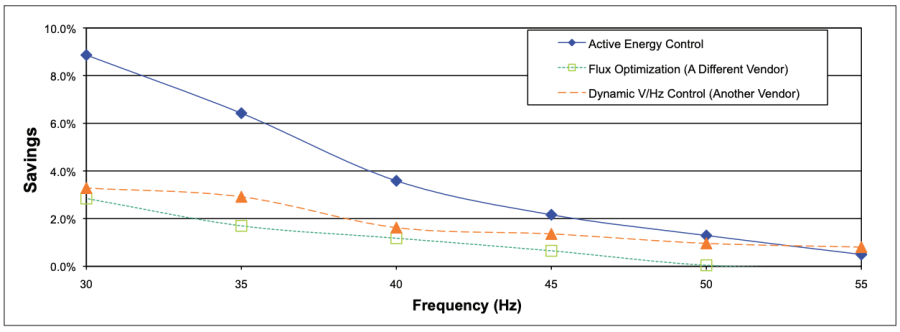
These results further prove that VFDs equipped with Eaton’s Active Energy Control algorithm outperform competing VFDs.
Improve the Efficiency and Stability of Your Motor Applications with Eaton and RS
VFDs are widely recognized as essential tools for improving energy efficiency in demanding commercial and industrial motor applications. But each supplier has at least a slightly different approach to VFD design and energy optimization, and both internal and third-party testing have proven that Eaton VFDs equipped with our patented Active Energy Control algorithm achieve superior energy savings compared with competitors’ static and dynamic V/Hz control methods.
Eaton has more than 100 years of experience developing intelligent power solutions engineered to improve the safety, efficiency, reliability, and sustainability of electrical, hydraulic, and mechanical power systems. So, you can trust us to deliver the innovative solutions you need to remain compliant and competitive.
Our proven Active Energy Control algorithm is built into our Eaton DM1, Eaton DG1, and Eaton HVAC DH1 VFDs. These drives are available at RS and are ideal for use with induction motors used to drive variable torque loads in applications including aeration blowers, air handling units, pumps, fans, and cooling towers used in HVAC and heat recovery ventilation (HRV) systems in demanding commercial and industrial environments ranging from data centers to hospitals and manufacturing facilities.
For assistance identifying, deploying, and maintaining Eaton VFDs optimized for your application, please contact your local RS representative at 1.866.433.5722 or reach out to the RS technical product support team.