PLC hardware and software often lag behind cutting-edge consumer technology to ensure reliability, but are rapidly gaining ground in many areas.
As noted in the recent Expert post about PLC Basics, programmable logic controllers (PLCs) are a mature technology at this point. This raises a few questions, such as:
- If PLCs are so mature, why aren’t they interoperable?
- If PLCs have been around so long, isn’t there something better by now?
- Are PLCs gaining smartphone-like capabilities?
To answer these and other questions, it’s necessary to look a little deeper into the hardware and software details making up contemporary PLC offerings. What we will find is that PLC platforms are so good at what they do exactly because of certain mission-specific qualities, with new features being added only after thorough testing.
What Do PLCs Do Best?
PLCs are basically heavy-duty programmable controllers that are easily connected to real-world sensors and devices to automate machinery and processes. They monitor input conditions, execute user program logic, command outputs, usually interface with operators in some way and may perform more complicated communications with other smart devices.
Over recent years, PLCs have followed the more open trend of consumer devices, becoming better about supporting standard Ethernet and USB connectivity, and using common industrial protocols like Modbus TCP and EtherNet/IP. However, there are still many closed or proprietary functions like configuration and programming, and these can rarely be transported among different makes and models of PLCs.
While the PLC market is relatively small compared to consumer electronics like PCs and smartphones, commercial PLCs are far more advanced and fit-for-purpose than niche hobbyist items like an Arduino or a Raspberry Pi. In particular, PLCs are built to withstand the harsh conditions often found where they are installed including extremes of temperature, vibration, electrical noise and environmental contaminants.
Picking the Right PLC Platform
Most suppliers offer a platform or ecosystem of PLC and/or human-machine interface (HMI) products that work well together. To pick the right platform, designers should consider the following points:
- Input/Output (I/O) types and count: The most basic deciding factor is choosing a platform supporting the needed I/O type and quantity.
- Scalability: Does the application need one PLC family that can be extended to handle small, medium and large systems?
- Custom systems: Is every project custom, best served by choosing the most flexible PLC to ensure it can perform?
- Value engineering: Is the primary need for mass-producing a machine where material costs must be driven down, driving selection of a platform just meeting requirements?
- Advanced features: Are any advanced features like communications to smart devices, HMIs or remote access needed?
- Costs and warranty: Not just the cost of the basic hardware, but also for the programming software or licensing, and possibly for ongoing support.
Choosing PLC Hardware
From PLC Basics, it was noted that PLC hardware typically consists of the following:
- Processor (or controller)
- Power supply
- Backplane/chassis (for modular PLCs); not applicable to brick PLCs
- I/O points
- Communication modules
Some PLC make/models have many options, while others are more streamlined offerings. Vendors usually publish a selection document, worksheet or at least a model comparison table to help end users make choices. Following are the top items to consider.
Processors are defined by their computing power, memory and I/O handling capacity. Many vendors provide estimating guides so that processor size can be selected based on the need. However, for all but the most complex applications, many users find that PLCs sized comfortably within rated I/O capacities will be sufficient.
Power supplies may require some estimating to ensure they are sized to handle the number of modules and type of I/O to be used, and the required modules must fit into slots available on the selected chassis.
I/O electrical details are quite important. Every I/O point has ratings for voltage, current, resolution (accuracy), sinking/sourcing configuration and isolation — all of which must be carefully matched to the application. Sometimes PLCs may not offer the exact right variant, which means interposing relays or signal converters will need to be added.
With the advent of smarter field devices and industrial internet of things (IIoT) sensors, advanced communications must be planned for and accommodated. Some fieldbus protocols require special modules and wiring, while other protocols might operate over industry-standard Ethernet.
Choosing PLC Software and Enhanced Capabilities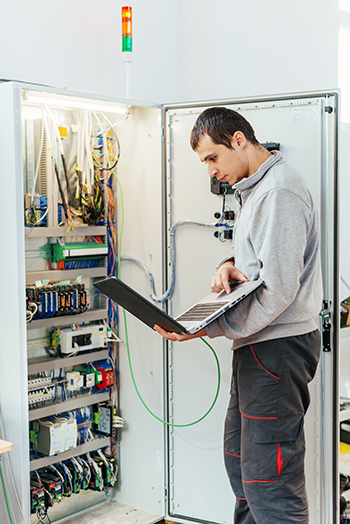
Although almost all PLCs will offer the same basic functionality, they each require specific programming software. Sometimes it’s free, and other times it costs extra. In some cases every make/model of PLC from a supplier has its own software, or perhaps one software package handles a variety of products, the preferred option.
Most basic PLCs are programmed in ladder logic, but there are other more advanced languages. Recently there has been a drive to adopt CODESYS as an industry-standard way to program PLCs, but this initiative is still gaining traction. Most PLC programming remains highly make/model-dependent, and therefore not portable without reprogramming, so it’s important for end users to stay within a product family.
Many PLC and HMI vendors provide remote accessibility. This may be via a network-connected browser or even a smartphone app. Mobile connectivity is rapidly becoming a popular way for users to remotely monitor, control and troubleshoot systems.
PLC Alternatives
PLCs are an excellent solution for almost any industrial automation need. For certain applications it may be possible to use commercial-grade microcontrollers like an Arduino or Raspberry Pi, however these are not proven for enduring industrial service and are very much do-it-yourself. On the other hand, there are some hybrid PLC products that may have unique features like small on-board user interfaces, and there are much newer products like edge programmable industrial controllers (EPIC) devices which offer PLC functionality plus full on-board HMI options and extensive communication abilities.